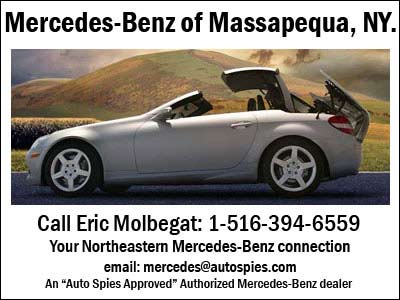
Mercedes-Benz presents the new eight-cylinder CDI engine: state-of-the-art technology for the finest in diesel-powered driving pleasure

World’s highest-torque passenger car diesel engine
Advanced lightweight aluminium construction
Newly developed biturbo system
Third-generation common-rail direct injection
Maintenance-free particulate filter fitted as standard
Developing output of 231 kW/314 hp and maximum torque nudging 730 Newton metres, the V8 diesel engine represents an impressive new chapter in the 70-year history of passenger car diesel engines at Mercedes-Benz. The new unit also underlines in emphatic fashion the expertise of the Stuttgart-based manufacturer in the development and production of state-of-the-art diesel engines. The new eight-cylinder unit is currently the world’s highest-torque diesel powerplant for a passenger car.
The newly developed V8 celebrates its premiere in the E-Class in autumn 2005 and will also be made available for other Mercedes-Benz passenger car model series in the future.
Boasting third-generation common-rail direct injection, piezo injectors, biturbocharging with variable turbine geometry, electrically controlled exhaust gas recirculation with bypass duct, water-cooled intercooler and a selection of other systems besides, the new eight-cylinder engine constitutes a unique package of high-tech innovations. Majestic power development, imposing torque, exemplary smooth running characteristics and low fuel consumption and exhaust emissions are all part of the service. Look no further for diesel-powered driving pleasure of the highest order.
A comparison with Mercedes-Benz’ previous eight-cylinder CDI engine highlights the main selling points of the V8 under the bonnet of the E 420 CDI:
Output: up 20 per cent
Torque: up 30 per cent
Added to which, the new power unit burns less fuel, despite its higher output, and meets the stringent EU-4 exhaust limits. The E 420 CDI is fitted as standard with a maintenance-free particulate filter system.
Aluminium crankcase: power-to-weight ratio cut by 13 per cent
A sand-cast aluminium crankcase forms the high-strength and remarkably durable basis for the new CDI engine. This material is a key factor in the engine’s impressive power-to-weight ratio of 1.12 kg/kW - 13 per cent below the value of its predecessor.
A bedplate construction ensures that the engine generates very little noise and low vibrations. The bedplate is an aluminium base section with integral grey cast iron inlays for the crankshaft main bearings. It supports the crank mechanism from underneath and provides additional structural rigidity. This helps to reduce longitudinal vibrations on the engine block extremely efficiently.
The pistons move along a 86-millimetre stroke in “wet” cylinder liners, which are in direct contact with the coolant and thus ensure that the crankcase is cooled as required. The pistons have also been newly developed, in order to withstand the high firing pressure (175 bar) inside the engine and to improve exhaust efficiency. To this end, a flat recess in the piston crown enhances the combustion process and helps to significantly reduce smoke emissions under full load. The supports for the piston rings have a special cooling duct and are oil-cooled – another new feature for a Mercedes-Benz passenger car diesel engine.
In the interests of keeping dimensions compact, the Mercedes engineers have arranged the cylinder banks at an angle of 75 degrees and fitted the eight-cylinder unit with a balancer shaft, which rotates in the opposite direction to the crankshaft and evens out vibrations. Likewise, the square stroke/bore ratio helps to give the new Mercedes diesel engine the smooth-running properties you would expect from an eight-cylinder unit. At the front end of the balancer shaft is an oil separator, which uses centrifugal force to act as a vent for the engine. The chain-driven device sucks gas containing oil out of the crankcase, before using gravity to filter out the oil. While the oil flows back into the engine, the gases move forwards out of the centrifuge and through a heated vent line into the intake pipe of the V8 engine. A valve takes care of the necessary pressure compensation.
The most important data of the new eight-cylinder CDI engine at a glance:
Cylinder arrangement V8
Cylinder angle 75°
Valves per cylinder 4
Displacement 3996 cc
Bore/stroke 86/86 mm
Distance between cylinders 97 mm
Compression ratio 17.0 : 1
Output 231 kW/314 hp at 3600 rpm
Max. torque 730 Nm at 2200 rpm
At 97 millimetres, the distance between the cylinders is the same as that in the previous Mercedes-Benz V8 diesel engine. The outstanding feature of the aluminium cylinder heads are the raised layers in the water jacket, which ensure impressive rigidity. A double-bush timing chain, which is lubricated by a separate oil sprayer, provides the drive for the exhaust camshafts. The distribution of oil over the chain allows it to be spread efficiently over the outer joint surfaces by centrifugal force. The intake and exhaust camshafts are connected by toothed gears, and the high-pressure pump in the common-rail injection system is also driven by toothed gear.
Air ducting optimises flow, pressure loss falls by 60 per cent
The two exhaust-gas turbochargers, which draw in and compress fresh air through the engine’s air filter, are located on the outer sides of the cylinder banks. Integrated hot-film air mass sensors supply the electronics with important basic information for the engine management. Another special feature developed by the Mercedes engineers are hollow inserts integrated into the intake lines, which increase the volume of the air before it enters the turbochargers. This raises torque output at lower engine speeds by up to 15 per cent.
The V8 engineers used sophisticated airflow calculations and simulations to reduce the loss of pressure typically experienced in the charge air manifolds of turbochargers and provide a sustained improvement in the supply of air to the new diesel engine. Under full load, the pressure loss is some 30 per cent lower in the charge air manifolds at the entry to the turbochargers than in Mercedes-Benz’ previous eight-cylinder CDI engine, and as much as 60 per cent lower in the charge air manifolds at the exit of the turbochargers. This means that an up to 15 per cent greater air mass can flow through the manifolds.
Improved VNT turbochargers: higher output coupled with reduced fuel consumption
Mercedes-Benz has also made further improvements to the turbochargers. These continue to work according to the proven VNT (Variable Nozzle Turbine) principle and are fitted with variably adjustable guide vanes, which alter their opening angle – and thus the flow area – according to the loads on the engine. This allows them to fully exploit the exhaust energy and create maximum charge pressure. Higher torque, lower exhaust gas backpressure under full load and low smoke output at high speeds are the principal advantages of variable turbochargers.
New vane geometry for the compressor and turbine wheels and the guide vanes makes the new engine more efficient than the previous eight-cylinder CDI unit, whilst the maximum permitted turbocharger speed has been further increased. These measures help to raise engine output and reduce fuel consumption, and the durability of the turbochargers under high temperatures has also been improved.
Majestic power development: 730 Newton metres as low as 2200 rpm
The exhaust-gas turbochargers play a key role in the exceptional torque and output of the new V8 engine. An electronic control system and dual air mass sensor allow the biturbo system to work in synchrony and adapts the supply of combustion air precisely to the output requirement. This enables the engine to develop over 580 Newton metres of torque as low down as some 1600 rpm – that’s 80 per cent of the maximum value (see diagram) and higher than the peak torque of its diesel predecessor. The new eight-cylinder unit develops over 700 Newton metres of pulling power at 1950 rpm, with maximum torque hitting 730 Newton metres at 2200 rpm.
Which all helps explain how the powerplant under the bonnet of the Mercedes-Benz E 420 CDI is capable of such remarkable performance figures. The Saloon accelerates from 0 to 100 km/h in just 6.1 seconds and completes the third-gear sprint from 60 to 120 km/h in 5.4 seconds. Below is an overview of the engine’s performance data:
Mercedes-Benz E 420 CDI*
Acceleration 0–100 km/h 6.1 s
Acceleration 60–120 km/h 5.4 s
Top speed 250 km/h*
Fuel consumption (combined) 9.3 l/100 km
*electronically governed
Enhanced charge air cooling: up to 25 per cent greater air density
In its previous V8 diesel engine, Mercedes-Benz used a water-cooled intercooler to cool the intake air compressed by the turbochargers. The new eight-cylinder is fitted with a further improved charge air cooler, which links up with a pair of water coolers to provide an even better basis for majestic output and torque development. The water-cooled intercooler fixed to the front of the engine reduces the air temperature by up to 120 degrees Celsius. Since cooler air has a higher density, the V8 power unit is supplied with a greater air mass and can thus develop more power. Under full loads, the highly efficient charge air cooling system increases air density by up to 25 per cent compared to the E-Class’ current V8 diesel engine.
The water-cooled intercooler is integrated into a special low-temperature water circuit, which also features a separate electrically-driven circulation pump. The low-temperature and main cooling-water circuits are connected by an expansion tank.
A bypass duct in front of the heat exchanger ensures more efficient exhaust gas recirculation
At the exit of the water-cooled intercooler, the charge air flows through an electrically activated throttle valve charged with the task of regulating exhaust gas recirculation. This valve helps to ensure extremely precise metering and mixing of the exhaust gas, which is recirculated into combustion air.
Exhaust gas recirculation makes a crucial combination to reducing nitrogen oxide emissions from the engine. The concentration of oxygen in the intake air is reduced by mixing in a precisely calculated proportion of the exhaust gases. As a result, the combustion temperature in the cylinders drops and lower quantities of nitrogen oxide are produced.
The amount of exhaust gas recirculated is dictated by the electronic engine management unit according to the loads on the eight-cylinder unit. The unit uses two recirculation valves – one per cylinder bank – which are controlled electrically via a solenoid. The exhaust gases flow together out of the two cylinder banks into a single-tube heat exchanger, which provides additional cooling. As this heat exchanger is not suitable for use in all situations, the Mercedes engineers have developed a bypass system, which opens as required and channels the exhaust gas past the heat exchanger. The recirculated exhaust gas is then mixed with fresh air and distributed to the eight cylinders through the charge air intake manifold.
Each cylinder is supplied with air through two inlet ducts. One of these is a spiral swirl port designed to generate a fast-moving swirl movement and the other a tangential port optimised to ensure effective filling and high output. The spiral swirl port whips up the air into a fast-moving swirl before it enters the cylinders, ensuring an optimum mixture of fuel and intake air under partial loads.
The latest in CDI technology: higher pressure and fast-working piezo injectors
Since common-rail direct injection made its debut back in 1997, Mercedes-Benz has introduced a constant stream of measures aimed at further developing and perfecting an already innovative system. The third generation of this technology, which lies at the heart of both the new eight-cylinder CDI engine and the recently introduced V6 diesel power unit, opens the door to a fresh wave of key improvements which help to reduce fuel consumption, exhaust emissions and combustion noise.
The new, inlet metered common-rail pump generates maximum injection pressure of 1600 bar, up from the previous 1350 bar. As in all CDI engines, this impressive pressure is at the driver’s disposal at all times – i.e. even at low engine speeds.
Another new feature are the piezo injectors for the engine’s eight combustion chambers. These are significantly lighter and work twice as fast as the solenoid valves used up to now. With a response time of just 0.1 milliseconds, the piezo injectors allow fuel injection to be adapted even more quickly and precisely to suit changing loads and engine speeds, helping to reduce emissions, fuel consumption and noise levels. Up to five injections of extremely small quantities of fuel are possible per power stroke, following one after the other in quick succession and with high precision.
At the core of the newly developed high-tech injectors is a piezo ceramic, whose crystalline structure alters in microseconds under an electric current. The development engineers used this effect, discovered by brothers Pierre and Jacques Curie in 1880, to raise the nozzle needle on the injector tip by just a few thousandths of a millimetre and thus to inject the fuel in a particularly fine spray.
A dual pilot injection system makes the engine easier on the ear
Pilot injection is another special feature which has always been part of Mercedes-Benz’ common-rail engines. This system enables smoother combustion, audibly reducing the noise levels generated by the direct-injection unit. This pre-injection process takes place once or twice in the new eight-cylinder CDI engine, depending on the engine load. In the space of less than a millisecond, small pilot quantities of fuel flow into the cylinders, ignite and pre-heat the combustion chambers. This helps to substantially reduce combustion noise during the main injection phase that follows.
Like the dual pilot injection system, the latest common-rail technology can call on double fuel post-injection. If necessary, the new Mercedes engine will use this facility to briefly raise the temperature of the exhaust gases in order to regenerate the standard-fitted particulate filter.
Newly developed control unit: a microcomputer governs all engine functions
Casting its watchful eye over fuel injection, the turbochargers, exhaust gas recirculation and virtually all the other engine functions is a newly developed electronic control unit located in the firewall area of the E 420 CDI. It is hooked up with other microcomputers via CAN (Controller Area Network) data bus and stores the data needed to tailor the responses of the eight-cylinder engine to the situation and requirements at hand. A major feature of this digital network is the torque harmonization interface. This is where the data transfer takes place between the engine and the Electronic Stability Program ESP®, which ensures that the eight-cylinder powerplant reduces torque when moving off on slippery ground or if the vehicle is in danger of skidding.
The microcomputer in the new CDI engine also controls all the functions of the common-rail system, including double pre and post-injection and the level of injection pressure. Overrun, charge pressure control, rev limiting and engine diagnosis are among the other tasks within the sphere of responsibility of the electronic control centre, which processes a wealth of data from signals and sensors.
A separate data bus links the engine management system with the generator and glow plug control device – the cornerstone of a newly developed quick-start glow system. This shortens the duration of the diesel engine’s preglow phase to the blink of an eye, putting the compression ignition engine on a par with its petrol-driven counterparts in this respect as well.
Effective emissions control: the catalytic converters and particulate filter work in tandem
State-of-the-art common-rail technology, electrically controlled exhaust gas recirculation and other facets of the engine team up to substantially reduce the eight-cylinder’s exhaust emissions. In addition, Mercedes-Benz has further enhanced the efficiency of the power unit’s emission control with two oxidizing catalytic converters and a particulate filter (all fitted as standard). This allows the new CDI engine to meet the stringent EU-4 exhaust limits.
The Stuttgart-based experts have taken steps to ensure that the exhaust manifolds also play a role in emissions control. The small mass of the manifolds, which are made of steel casting, allows them to heat up quickly after a cold start and thus also to cut the response time of the catalytic converters, which are activated after the engine is started. The emission control systems each have a capacity of around two litres and break down a large proportion of the unburned hydrocarbons and carbon monoxide though a chemical reaction with oxygen (oxidation).
Behind the catalytic converters are the two exhaust manifolds which lead to the particulate filter (4.5 litres). This filter is regenerated without the need for additives and thus remains effective over an extremely high mileage. Similarly to the catalytic converters, a large number of rectangular cells run lengthways through the diesel particulate filter. By contrast to the catalytic converters, however, the cells in the particulate filter are sealed at either end. The in-flowing exhaust gas therefore has to find its way through the porous partition walls. In so doing, the carbon particulates contained in the exhaust gases are deposited in the filter, where they are retained.
The particulates in the filter are burned off in a controlled process and without the driver or other road users noticing. This process can involve either the hot exhaust gas generated at higher engine speeds or certain engine functions, such as double fuel post-injection, which are activated in response to the loads on the engine and the condition of the filter.
After passing through the diesel particulate filter, the exhaust gas is led once again through two ducts to the two mufflers.
Oil sump sensor: service intervals of up to 40,000 kilometres
The new V8 compression ignition engine is fitted with a sensor in the oil sump, which sends back data on the level, quality and temperature of the engine oil, among other things. On the basis of this information, the service interval indicator ASSYST can detect how the quality of the oil is changing and creates a tailor-made service plan for the engine, which also records any oil changes.
A digital display in the instrument cluster informs the driver how many kilometres remain until a change of engine oil is required and how many days or weeks he or she can drive up to that point. This service interval indicator enables the E 420 CDI to meet oil change intervals of up to 40,000 kilometres or two years, depending on driving style and engine load.
In addition, the sensor makes checking the oil level that much easier. After filling up with fuel, all the driver has to do is press a button on the multifunction steering wheel and information will appear on the central display in the instrument cluster highlighting the oil level and how much oil, if any, is required.

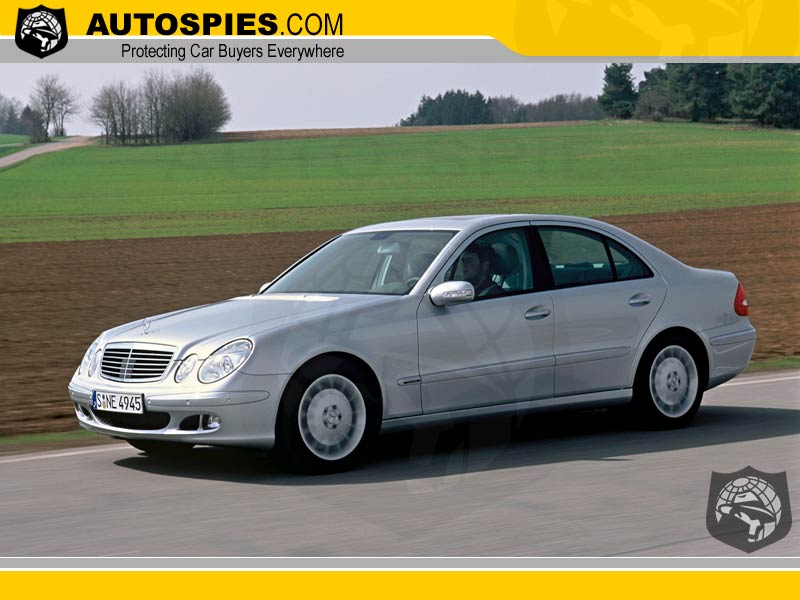
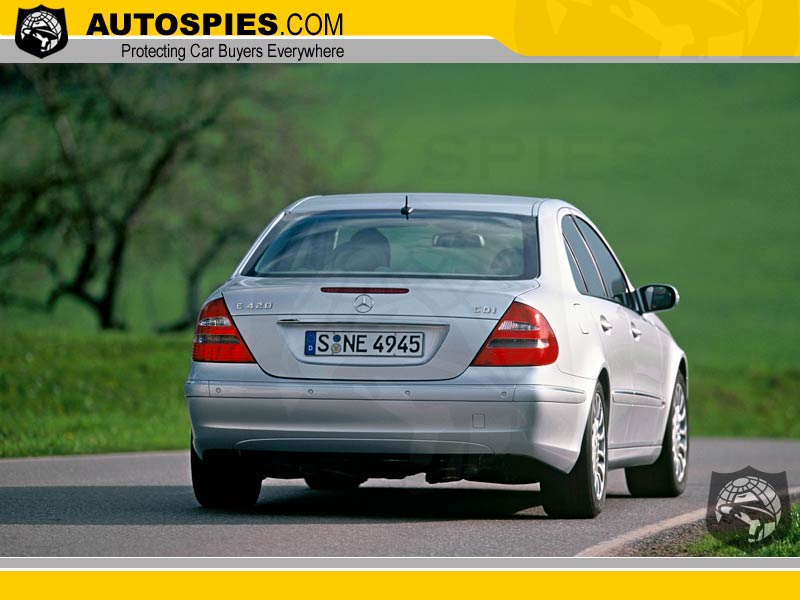
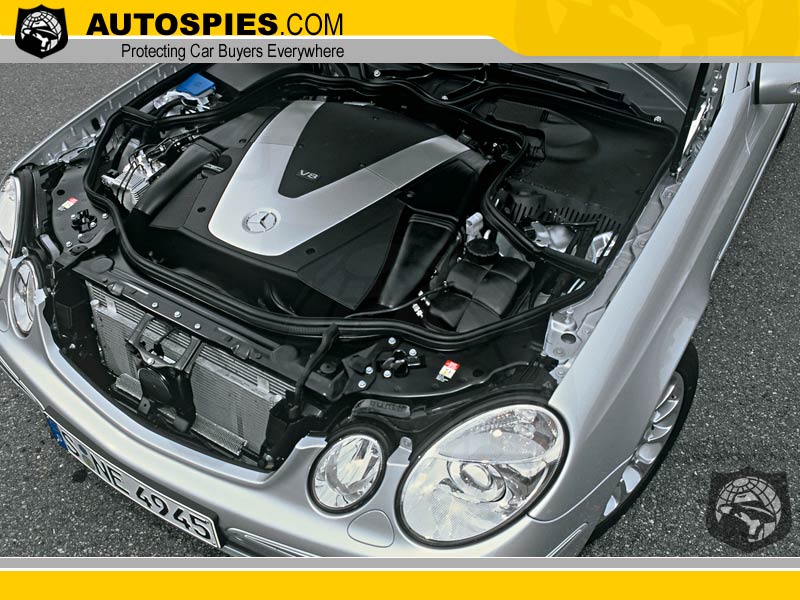
Click here to view part two