Greetings from Stuttgart!
At least that's what I would expect Agent 001 to say to you if he were writing this. As he is preparing for the 2011 Geneva Motor Show, 001 was at the Audi lightweight design tech days and the Audi Forum.
One complaint that has been held over Audi's products in recent years is that they always bore some heft and were not exactly nimble. But 001 reports to me that after experiencing the latest and greatest from Audi at their tech days that the new designs drive NOTHING like their heavier siblings.
According to 001, there is an extreme makeover under way and that drivers familiar with BMW will be pleased to get behind the wheel of Audi's newest products. The proof is in the pudding as 001 recently announced that the new 2012 A6 is at the top of its class.
Finally, he relays to me that the most impressive drive was the Audi Quattro Concept showcar, which was disguised in a current-generation A5 shell. 001 says that with the weight reduction it "feels very similar to the drive of a 911."
Considering 001 owns a 911, I think he would have a pretty good handle on that car's feel.
Audi Lightweight Tech Showcase Photo Gallery
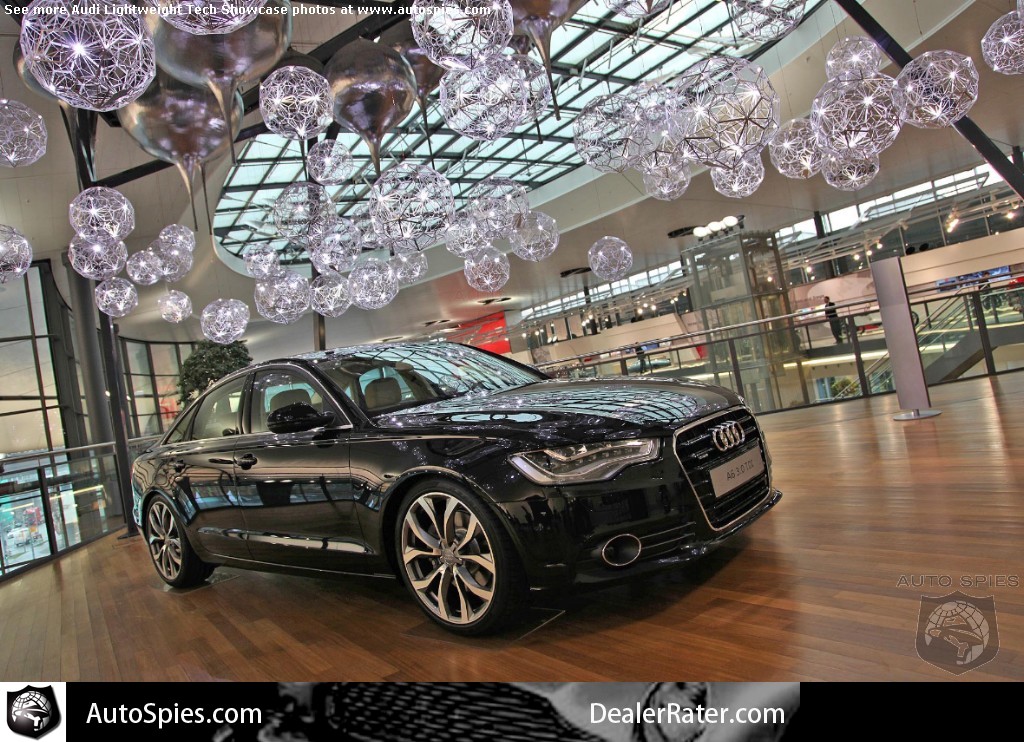
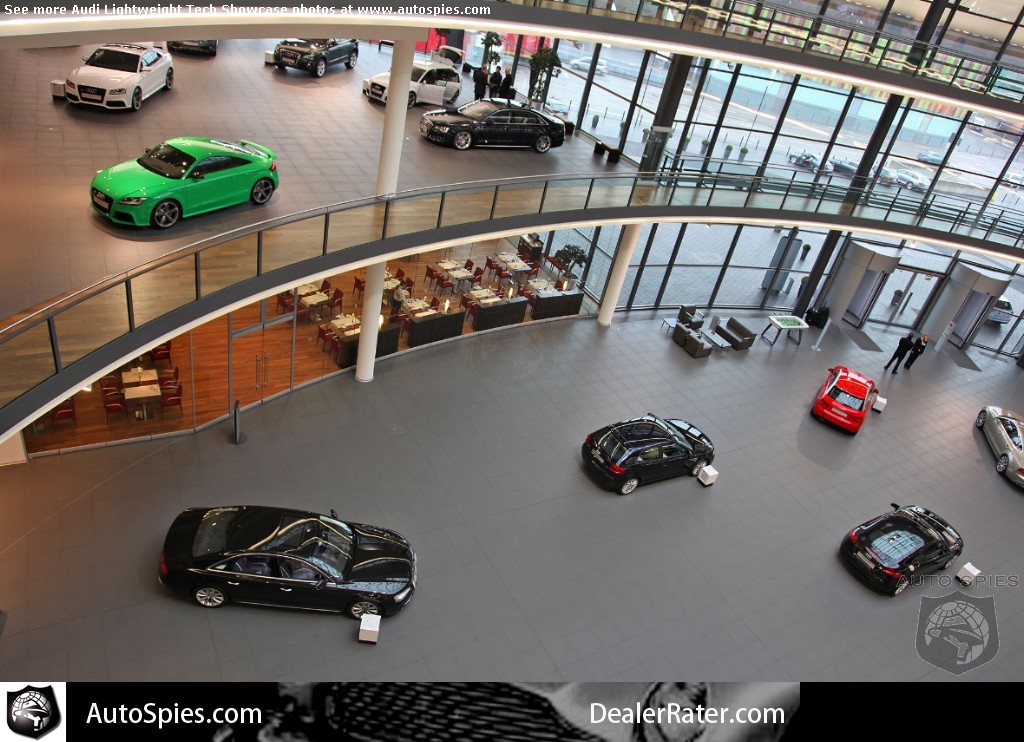
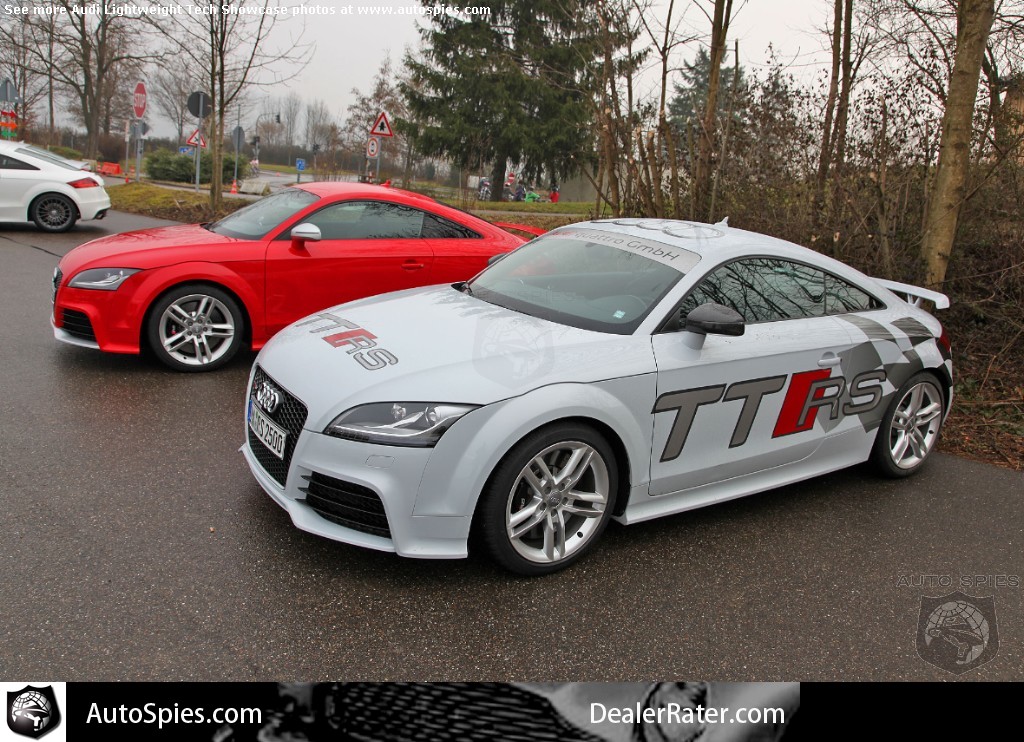
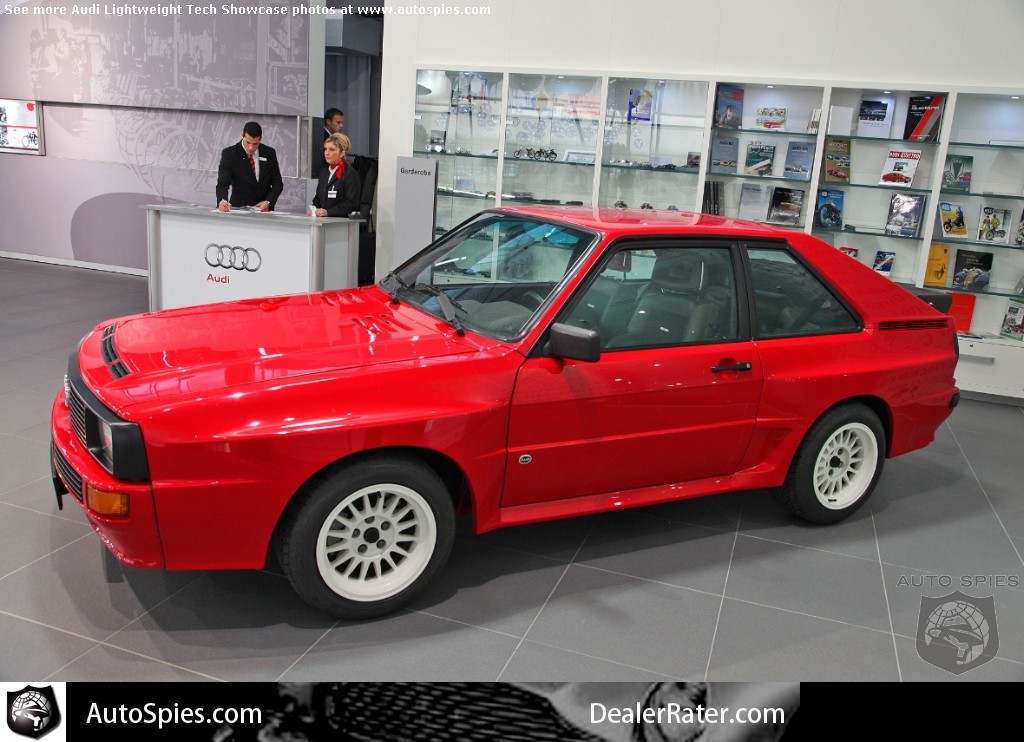
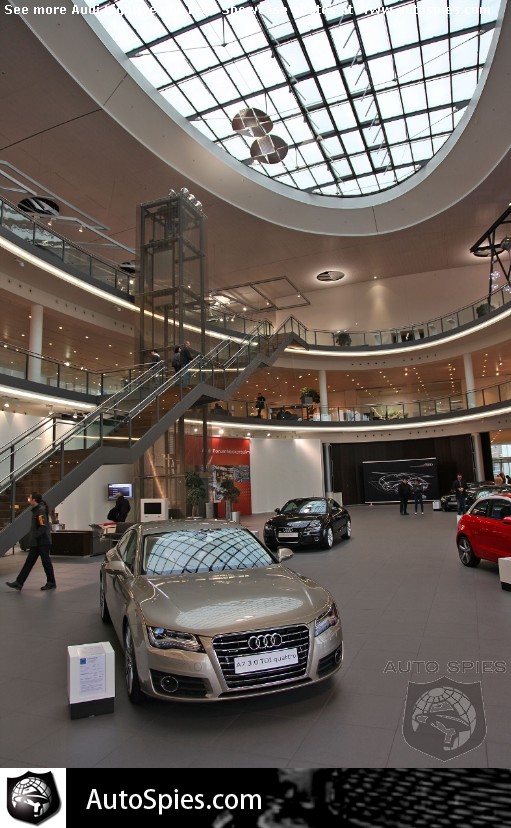
Audi's press release follows:
Light cars in large volumes – an Audi core competence
Lightweight construction has long been a top priority at Audi; it is one of the pillars of the brand. As the pioneer of the self-supporting aluminum body, Audi is the worldwide leader in the field of lightweight construction. Future innovations will ensure that the brand can continue to reverse the weight spiral. Each new Audi model will be lighter than the one it replaces.
Audi’s lightweight construction approach is a philosophy embraced by every development engineer. It begins with the body and emanates outward to include every area of technology in the complete vehicle, from the engine to the wiring harness. And it is not just the aluminum bodies featuring the Audi Space Frame (ASF) design that are unusually light. A number of volume models with steel bodies also set the standard in their respective class.
When it introduced the first A8 in 1994, Audi had not only developed the ASF design and put it into series production, it had also developed all of the steps required for its production. This integrated approach was what made this breakthrough possible. Audi gradually expanded its competences, adding numerous high-tech fabrication processes, in particular.
The brand takes a holistic and sustainable approach to this field of technology that encompasses the entire development and production chain. For Audi, lightweight construction not only means material engineering, it also means full competence in process technology, the development of new joining technologies and the validation of service and repair options.
Lightweight construction in large volumes is an Audi core competence. Since 1994, the company has continuously produced vehicles with ASF bodies. The number now totals 550.000, far more than any other manufacturer in the world. In the current model lineup, the A8 luxury sedan and the R8 high-performance sports car represent the ASF principle in its purest form. The body of the TT compact sports car is a hybrid aluminum and steel construction, and the A7 Sportback and the new A6 have steel bodies with a large fraction of aluminum.
The evolution of the Audi Space Frame Audi is now taking the ASF principle to the next level – the Multimaterial Space Frame. This combines aluminum, steel and fiber-reinforced plastics. While still a space frame construction, this involves the use of some new joining technologies.
What makes the space frame principle so impressively elegant from a technical perspective is that separates the tasks of the various components of the body. The extruded sections bridge spaces, the cast nodes connect the components, the aluminum panels close off the spaces and lend rigidity to the framework. The space frame principle assigns a specific task to each material and each component. This gives the development engineers much more freedom than the traditional monocoque sheet metal design.
Audi is convinced that the Multimaterial Space Frame is the right approach for building vehicles in high volumes. Compared to a CFRP body, it is just as good, if not better with respect to weight, and it offers major advantages, not the least of which are a better overall energy balance and the lower costs.
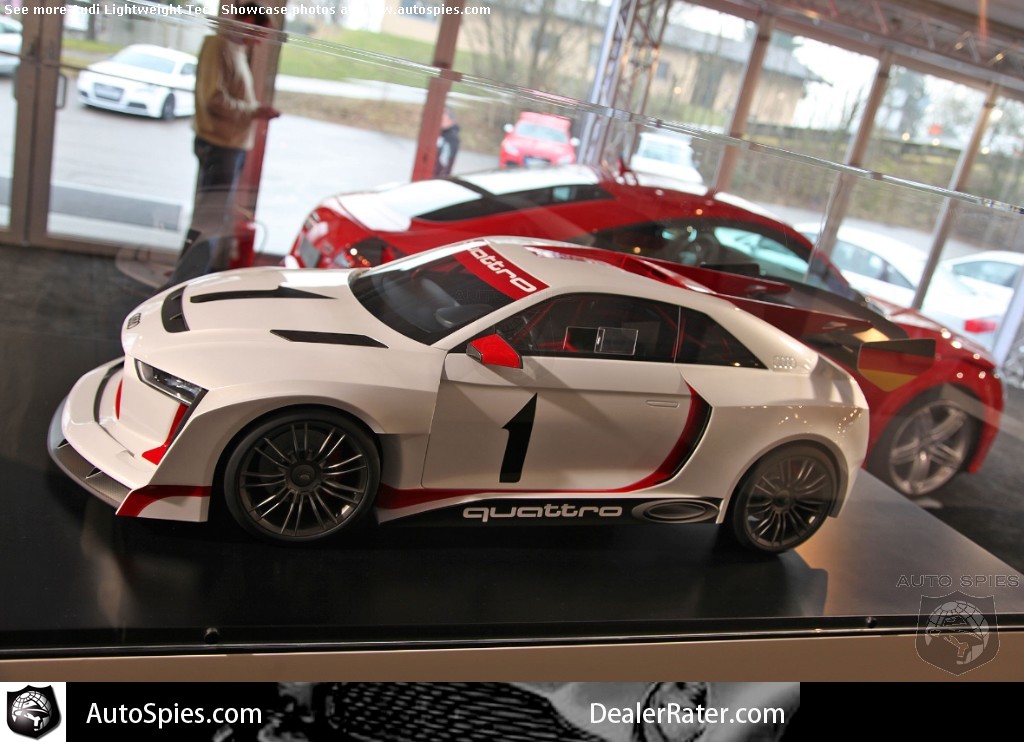
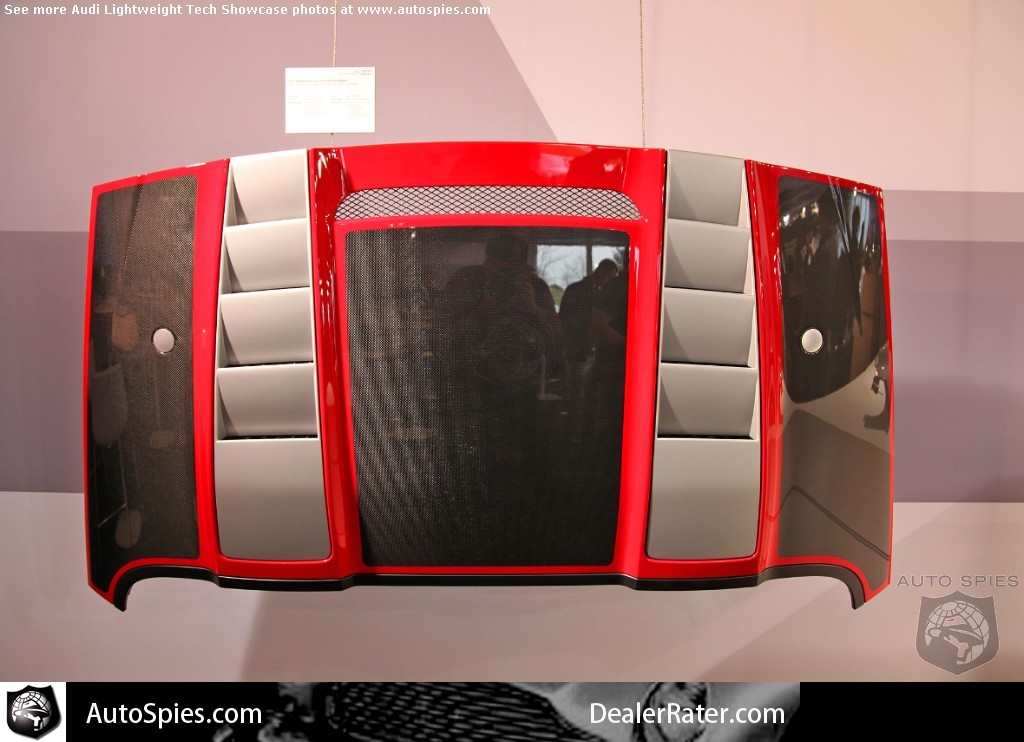
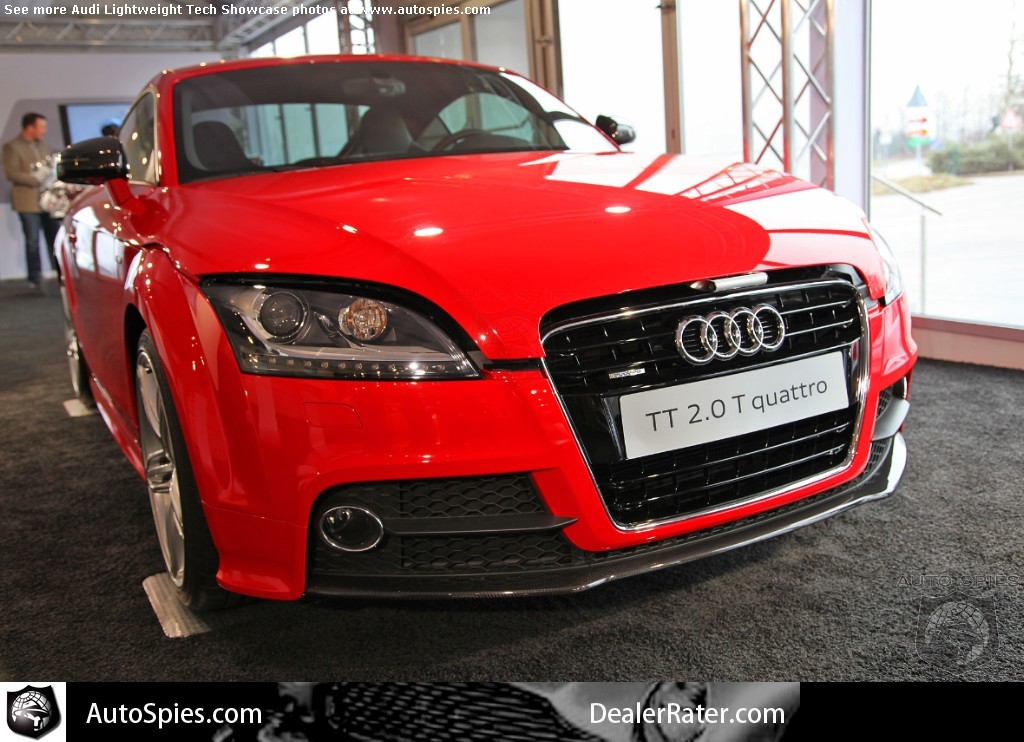
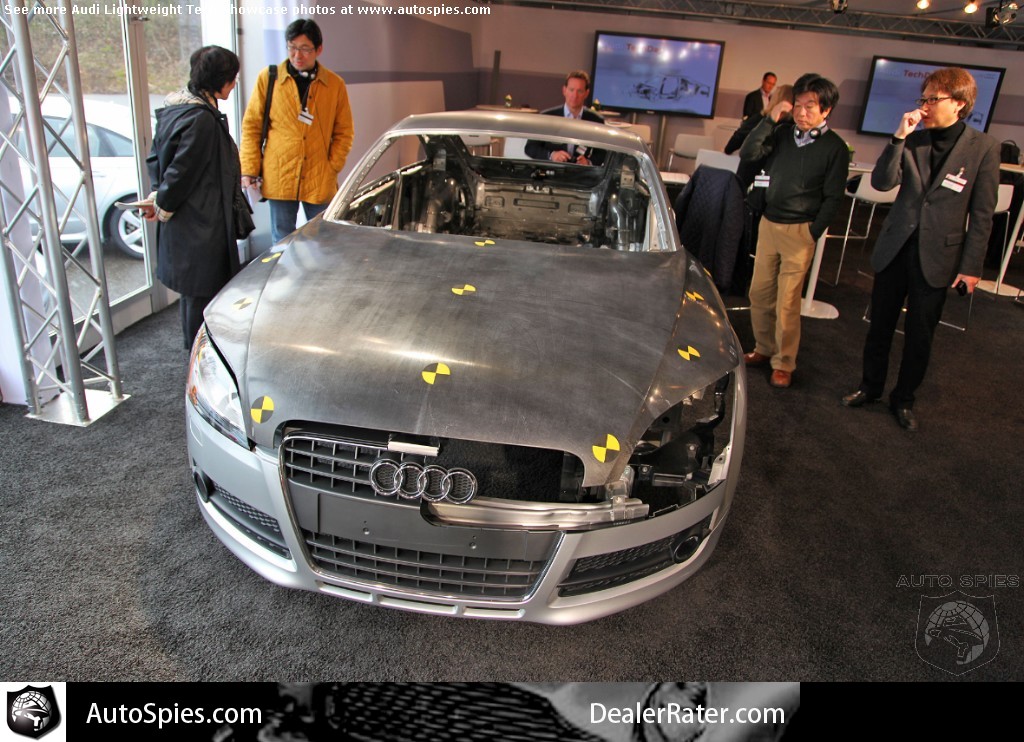
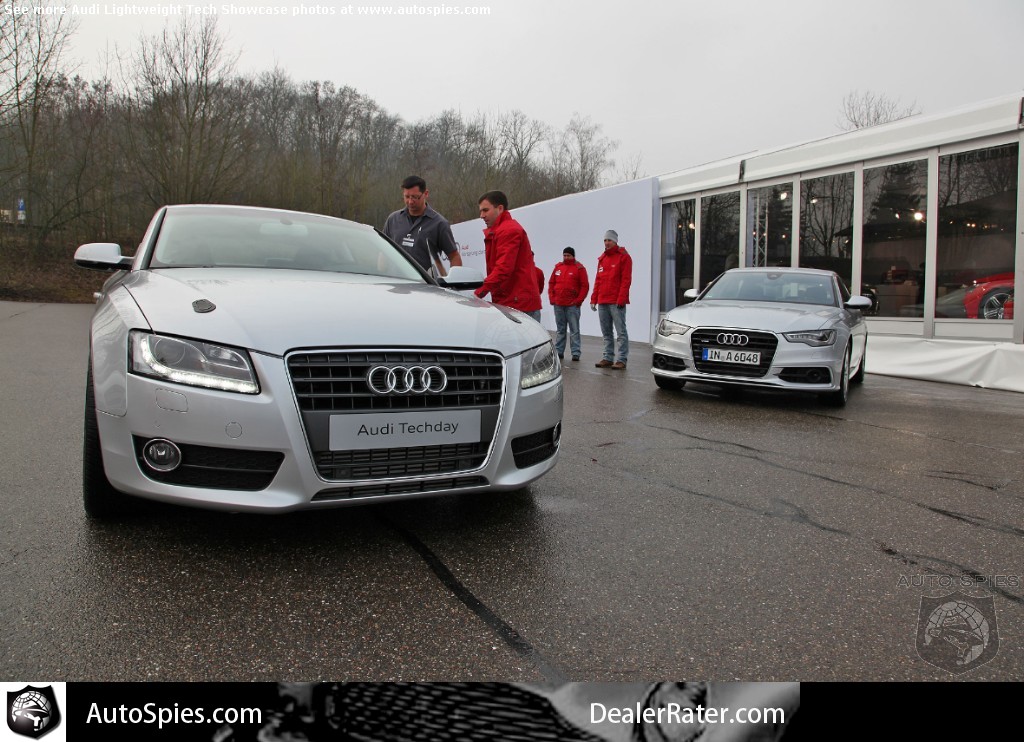
Wide-ranging materials competence
At Audi, lightweight construction does not mean the rigid fixation on a single material, but rather working intelligently and flexibly with diverse materials. Our motto is, “The right material at the right place for optimal function.”
The objective is to achieve the best performance while using the least amount of material possible, but using it at the right place. Just like in nature, where material is not wasted, either. The engineers have developed wide-ranging expertise in all of the relevant fields of technology. Every material, whether steel, aluminum or fiber-reinforced plastic, is repeatedly reviewed for it suitability for the intended purpose, and the Audi experts are intimately familiar with their potential and weaknesses.
The materials are in competition with one another, and Audi can use any and all advancements to its direct advantage. With aluminum, for instance, new high-strength alloys and further refined component structures will result in significant progress very soon. In the medium term, CFRP components will make the structure of the ASF even stronger, lighter and safer. Audi can use precise simulations to accurately compute the crash properties of this material.
The Audi Lightweight Design Center
The primary source of this broad-based competence is the Audi Lightweight Design Center. Roughly 180 specialists work at the facility. The ALDC is the company’s spearhead in lightweight construction. The lessons learned here have so far provided the basis for numerous patents, for the honor of European Inventor of the Year 2008 by the European Patent Office, and for four wins in the Euro Car Body Award, the world’s most important competition in car body design.
Some 50 experts in the FRP Technical Center are now focusing their efforts on fiber-reinforced plastics. Audi is engaged in a lively technology transfer with its sister brand Lamborghini in the fields of CFRP and aluminum, with both sides continuously gaining new insights.
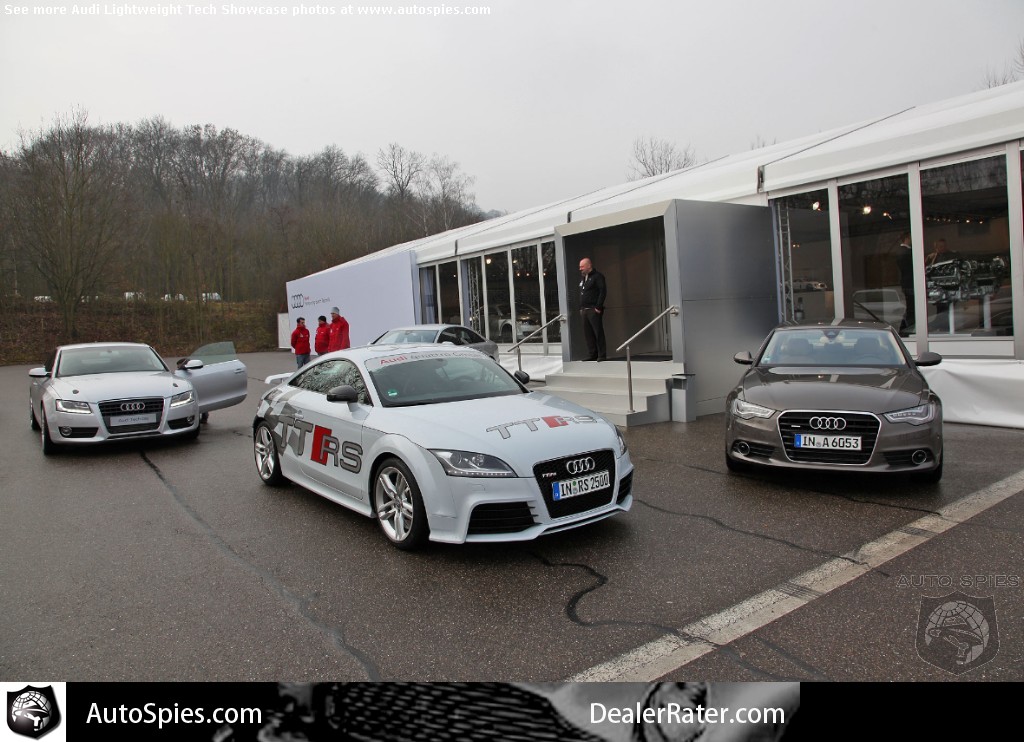
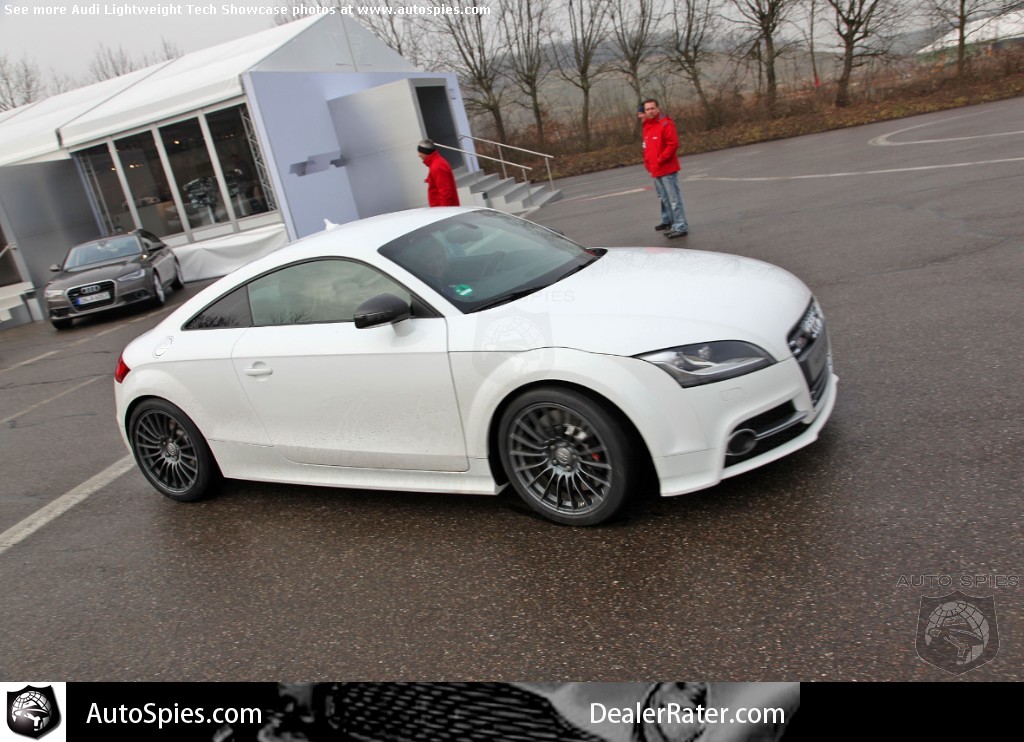
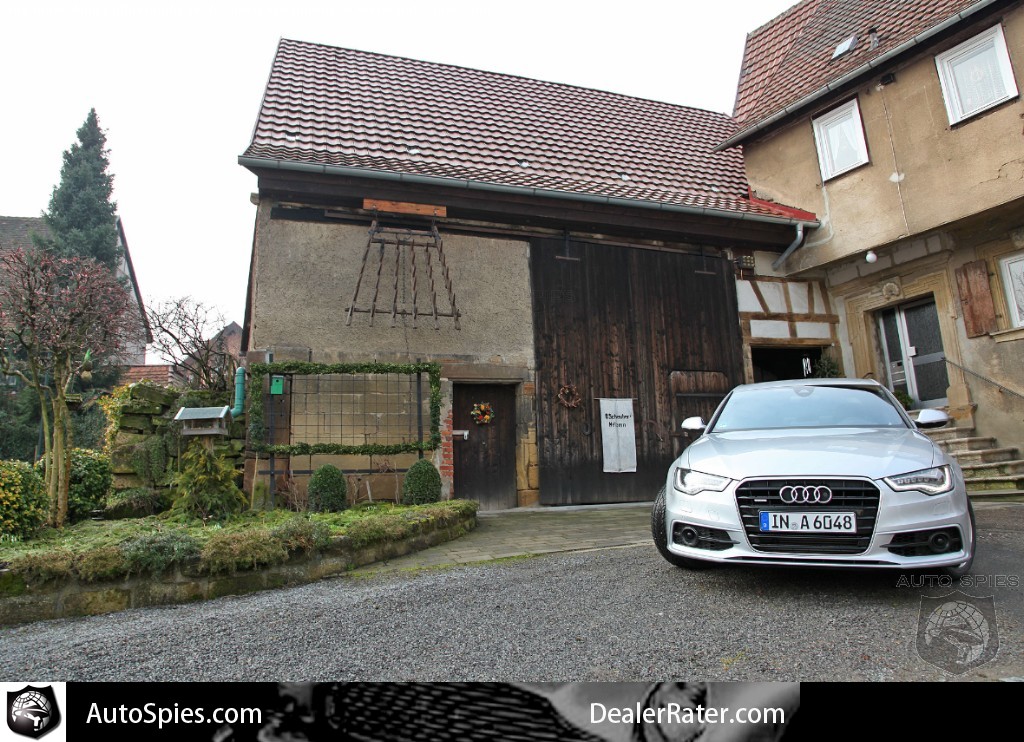
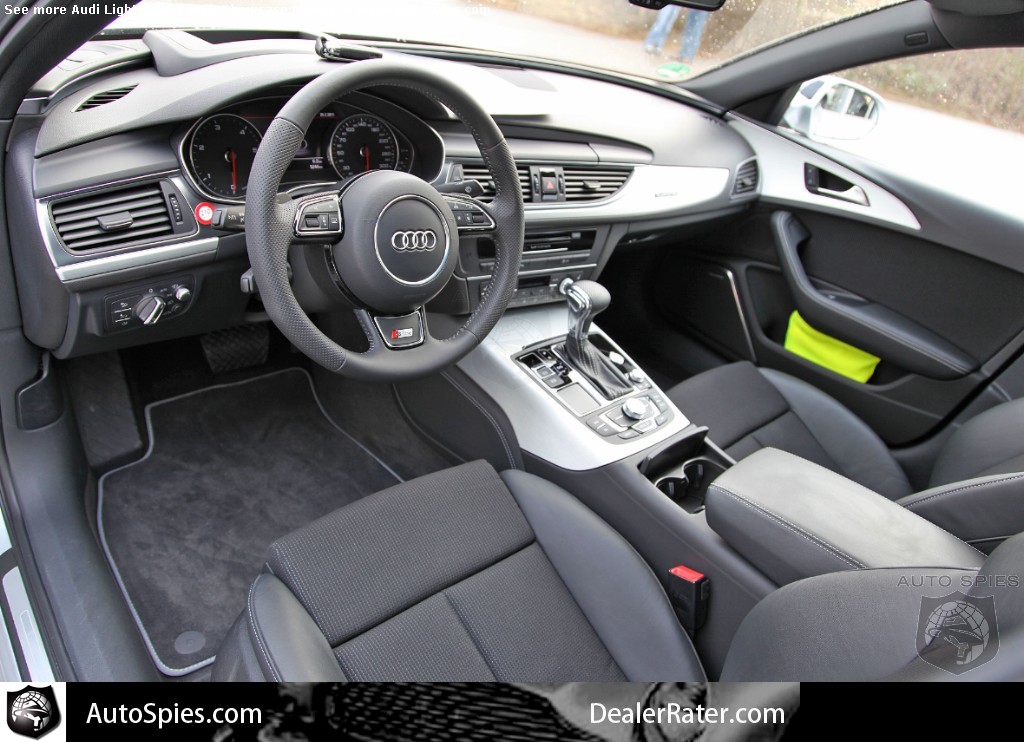
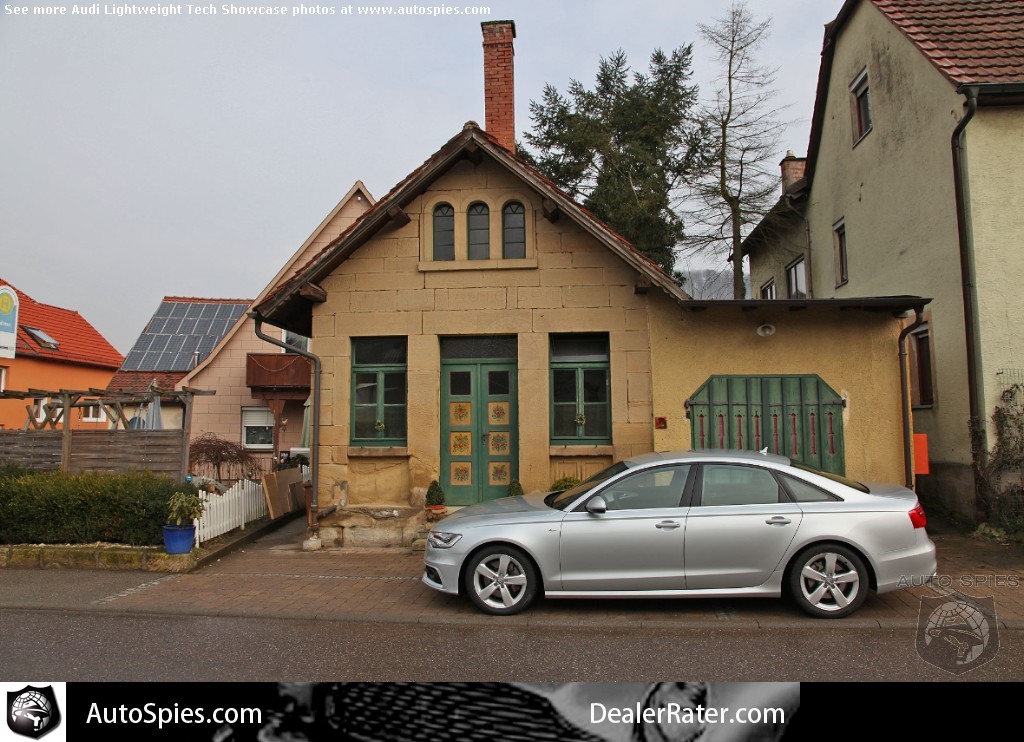
A century of lightweight construction
Lightweight construction has a long tradition at Audi and its predecessor companies. In 1913, NSU built the Type 8/24, a model having a body made entirely of aluminum. Ten years later, the Audi Type K wore an experimental streamlined skin of this same material.
In the 1930s, specialists from the Racing department of Auto Union shaped aluminum panels by hand, from which the bodies and streamlining panels for their spectacular race cars and land speed record cars were built. The 1936 Auto Union Type C tipped the scales at just 825 kilograms
(1,327.71 lb) ready to race. With its V16 supercharged engine producing a good 280 kW (520 hp), it had a power-to-weight ratio very close to that of a modern Le Mans sports prototype.
Audi continues to drive progress on the racetrack today. The rally and circuit race cars in the years around 1990 included many plastic parts in and on the body. Some of them were already using cardan shafts of carbon fiber composites at that time. This was already a standard feature on the
Audi 90 quattro. Today the Audi R18 and the A4 DTM serve as rolling labs for working with CFRP.
Coming to production vehicles, the first Audi A8 caused quite a stir upon its debut in 1994. With its ASF body, the A8 incited a minor revolution in the rather conservative steel and castings industry and placed suppliers under tremendous pressure. Since then, the strength of high-strength steels has increased by a factor of 5, and foundries have made significant gains in quality standards. The Audi ASF principle has benefited not just the brand’s customers, but the entire industry.
Lightweight construction will again play a crucial role in electric mobility of the future. New components such as the traction battery contribute a substantial amount of additional weight, and intelligent lightweight construction can compensate for this in many areas. The engineers in Neckarsulm are already working to develop entirely new solutions for the bodies of future electric vehicles.
Groundbreaking innovations – lightweight construction in the future
The future of lightweight construction has already begun at Audi. The Audi Lightweight Design Center (ALDC) is working intensely on improved and new materials, methods and processes. The facility was expanded in 2010 to include a FRP Technical Center focused on fiber-reinforced plastics (CFRP).
Audi is pursing a highly integrated strategy with lightweight construction. The brand's experts collaborate closely with universities and research institutions. Together with preferred producers of raw materials and selected suppliers, innovative lightweight solutions are developed until they are ready for series production. This is just as true for carbon fiber-reinforced plastics as it is for aluminum, steel and magnesium.
As they strive for new solutions, Audi engineers are also driving the competition between the materials. The classic metals still harbor a lot of intriguing potential. Potential that can be tapped with new joining techniques, by optimizing their technologies and with new alloys that further increase strength, thus lowering weight. FRP materials, headed by CFRP, can reinforce metal components or even replace them in some areas. They hold promise for many innovative solutions for the electric vehicles of the future. The Audi Group leads the competition when ot comes to crash simulation with CFRP materialy.
Audi is already working to take ASF technology to the next level. The Multimaterial Space Frame combines all of these materials together in different ways depending on the model. In the medium term, the new ASF body structures will replace the traditional monocoque steel bodies at Audi. The new construction will once again greatly reduce weight.
Audi lightweight construction – the reversal of the weight spiral
Throughout almost the entire automobile industry, vehicles are getting steadily heavier from generation to generation. This has been the case for many years now. Not at Audi, however. The brand with the four rings is reversing the weight spiral with its systematic strategy of lightweight construction. The second generation of the TT compact sports car tips the scales up to 90 kilograms (44.09 and 198.42 lb) less than its predecessor. With the new A6 currently being launched, this difference can be as much as 80 kilograms (176.37 lb), depending on the model. Each new Audi model will continue to be lighter than its predecessor.
The lightweight construction principle practiced by Audi conserves resources, lowers fuel consumption and thus enhances economy. Depending on the engine, the new A6 consumes as much as 21 percent less fuel than its predecessor. Lightweight construction accounts for roughly one-fifth of this progress. Generally speaking, shaving 100 kilograms (220.46 lb) of weight reduces fuel consumption by between 0.3 and 0.5 liters per 100 km.
At Audi, lightweight construction begins with the body, which brings with it an array of secondary effects throughout the rest of the car. A lower body weight enables the use of more compact brakes, a smaller engine, a correspondingly trim exhaust system and a smaller fuel tank. The individual components also harbor a lot of potential for saving weight. Lightweight gas springs are sufficient for a lighter aluminum rear hatch, for example.
Lightweight construction also offers decisive advantages with respect to sportiness, driving safety and comfort. A car weighing 1,200 kilograms (2,645.55 lb) reaches the 100 km/h (62.14 mph) mark from a standing start 6 meters (39.37 ft) sooner than a vehicle weighing 1,300 kilograms (2,866.01 lb). The reduction of so-called rotating masses with their moments of inertia has a particularly strong effect on acceleration.
A lower vehicle mass also has many positive effects on braking. Stopping distance is shorter and less heat is generated. The lighter a car is, the less kinetic energy it develops and the less of this energy needs to be converted into deformation in the event of a crash. In the event of a collision, less load is also exerted on the other vehicle involved.
One particularly interesting field of technology is lightweight construction in the chassis. The reduction of the unsprung masses at the wheels makes it possible, for example, to build lighter suspension components.
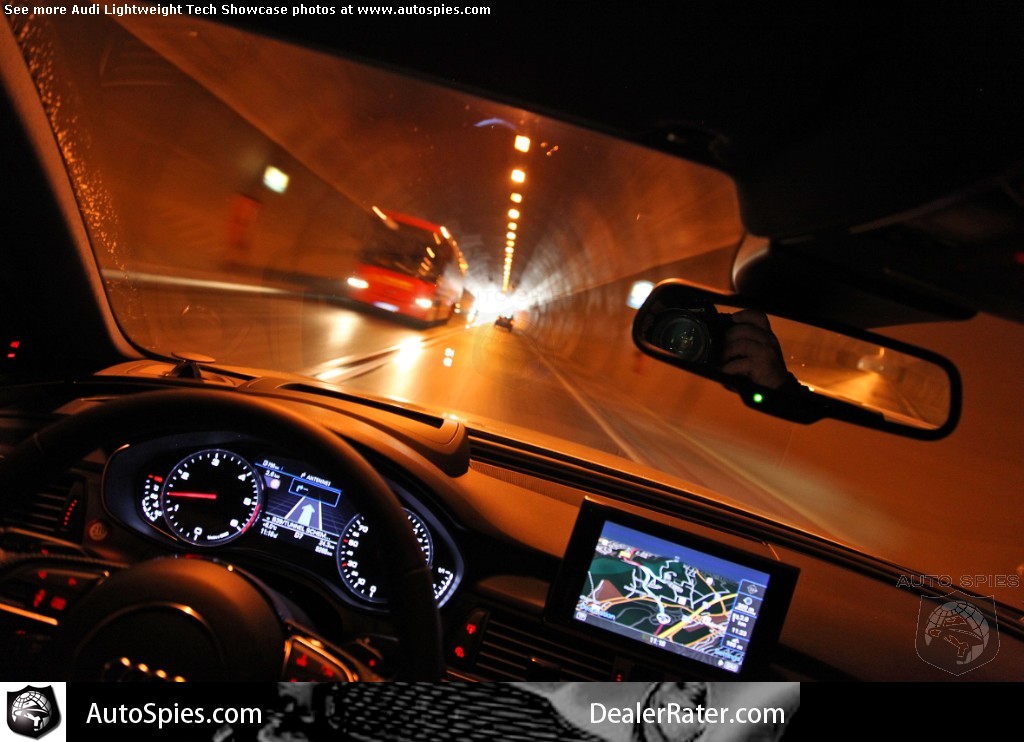
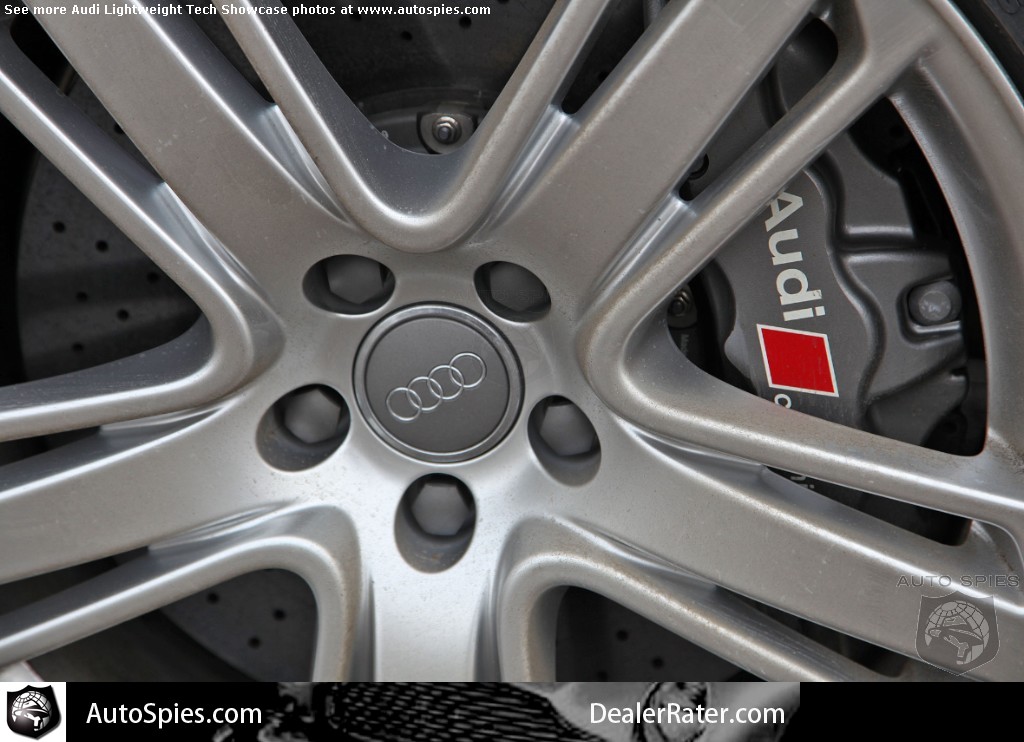
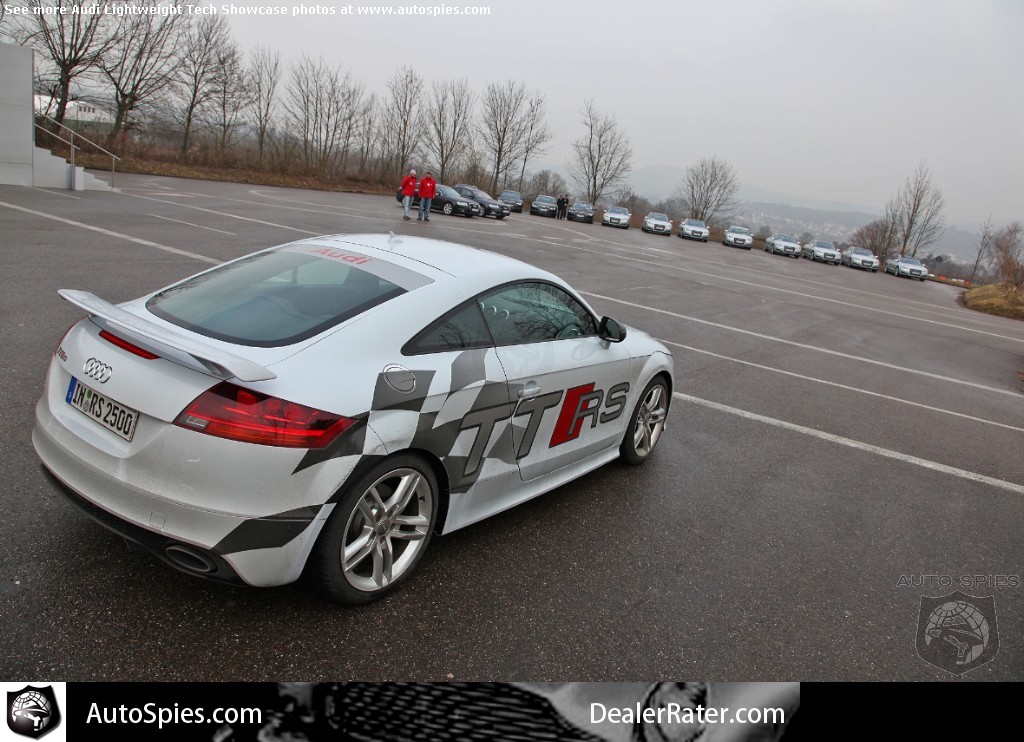
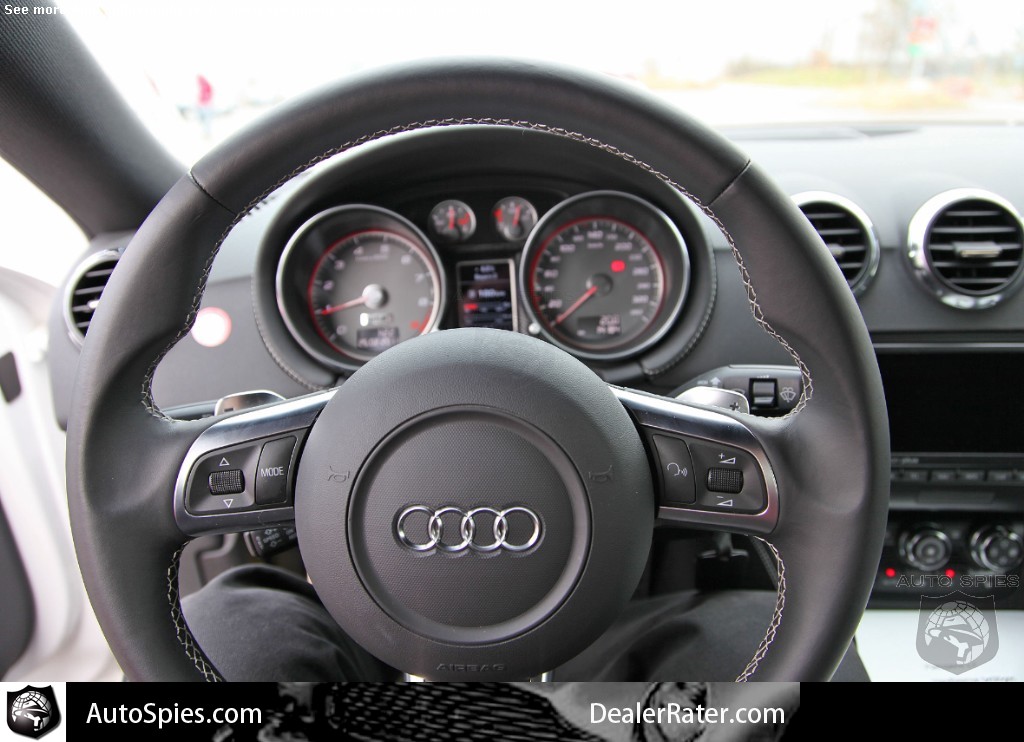
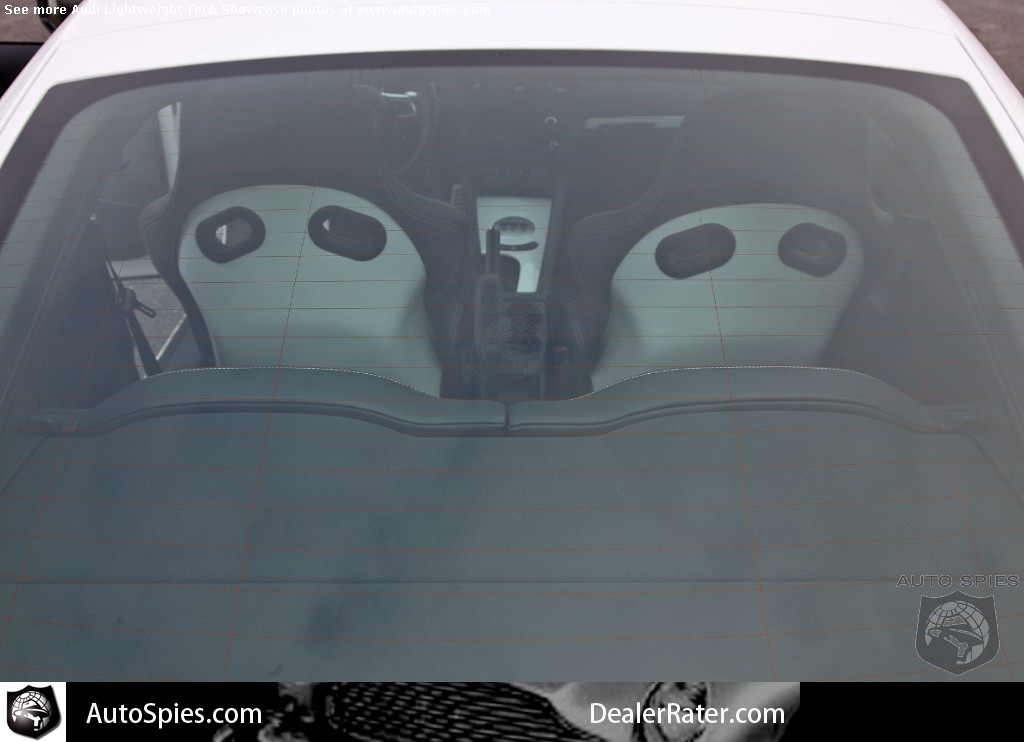
Lightweight construction with continuity: Audi milestones
Lightweight construction has long been a driving force at Audi. Development work on the ASF body began back in the early 1980s. Audi has been building cars with aluminum bodies since 1994 – with a high degree of continuity, in contrast to its competitors.
Audi Sport quattro (1984)
The Sport quattro is a brand icon. Beginning in 1984, Audi built 214 units by hand in order to homologize its new competition car for the Rally World Championship. The five-cylinder turbo, which displaced just 2.1 liters, produced 225 kW (306 hp) in the street version, making it one of a small group of extreme sports cars at the time.
The Sport quattro had a wheelbase that was 32 centimeters (1.05 ft) shorter than that of the model on which it was based, the Ur-quattro (original quattro). 4.16 meters (13.65 ft) long, it weighed just 1,300 kilograms (2,866.01 lb) thanks to extreme lightweight construction. Only the bodyshell and the doors of the “Shorty,” the latter taken from the Audi 80, were made of steel sheet. The rear hatch was made of a polyester material.
Most of the body components – the front and rear fenders, the front skirt, the hood, the outer shells of the B- and C-pillars, the roof and the rear skirt – were made of a material developed specifically for the project. This was a resin laminate into which multiple woven elements of aramid and glass fiber were embedded. Audi developed many new technologies for working with this material, from presses to high-pressure water cutting to joining with screws, rivets and adhesive.
The aramid composite material achieved nearly the same torsional rigidity as conventional steel sheet, but was almost three times lighter. The weight of the body was reduced by 64.2 kilograms (141.54 lb). The hood was additionally reinforced with carbon fiber in the area cutout for the intercooler. It cost DM 3,500 as an individual part.
The Audi A8 (1994)
Lightweight construction took on the rank of a strategic project at Audi in 1982. The objective meant reinventing the self-supporting body with a new material and a geometry specifically tailored to it.
The development work was extensive and resulted in 40 patents and patent applications in addition to broad-based fundamental expertise. In 1985, Audi presented the body of an Audi 100 made of aluminum but still using a traditional monocoque design. The concept sports cars from 1991, the Audi Avus quattro and the Audi quattro Spyder, also had skins of the light metal but underneath were still supporting frames.
The new technology was ready for series production in 1993, however. A shining silver showcar with an unpainted body of polished aluminum was on display at the International Motor Show in Frankfurt am Main, Germany. The predecessor to the A8 bore the designation ASF, the abbreviation for Audi Space Frame.
The production model that debuted the following year was the world’s first large-volume production car with a self-supporting aluminum body. The superstructure of the A8 weighed just 249 kilograms (548.95 lb) and featured the same construction that is still used today. Panels accounted for most of its 336 individual components, followed by the sections and castings. Assembly was performed roughly 75 percent by hand.
The Audi A2 (2000)
The Audi A2 was the second Audi ASF model. Just 3.83 meters (12.57 ft) long, it boasted agile performance and amazing efficiency. The base model of the small van weighed only 895 kilograms (1,973.14 lb). The A2 1.2 TDI, the world’s first five-door three-liter car, weighed just 825 kilograms (1,818.81 lb). Its average fuel consumption of 2.99 liters/100 km (78.67 US mpg) remains unsurpassed today.
The key factor in this was the aluminum body, which tipped the scales at just 156 kilograms (343.92 lb). Designed for higher volumes than the A8, it used important refinements and new developments in the areas of tools, casting and joining processes. The number of individual parts was reduced to 238. The B-pillar, for instance, comprised a single large casting. The B-pillar of the luxury sedan was still assembled from eight components.
Aluminum panels also accounted for the greatest share of semi-finished components in the A2, followed by sections and castings. The underbody frame was made up of straight extruded sections that were joined directly together by means of MIG welding (MIG = metal inert gas), eliminating the nodes required in the A8. Three joining processes, including state-of-the-art laser welding, sufficed for assembly. The degree of automation reached roughly 85 percent.
The Audi TT (2006)
The second generation of the TT features a groundbreaking Audi innovation – hybrid aluminum and steel construction. The front end, the floor and the superstructure of the compact sports car are made of aluminum, with deep drawn steel being used for the doors and the trunk lid. The rear section of the floor assembly, the tail panel and the bulkhead of the Roadster are made of high-strength steel. This material mix provides for an optimal distribution of axle loads and thus for dynamic handling.
The ASF body of the TT Coupé weighs in at 206 kilograms (454.15 lb); that of the TT Roadster at 251 kilograms (553.36 lb). Compared to the previous model with its steel body, the curb weight decreased by 20 to 90 kilograms (44.09 to 198.42 lb) depending on the model. Audi reversed the weight spiral. The material mix is dominated by aluminum, which accounts for 68 percent of the Coupé’s weight and 58 percent of the Roadster’s. In the TT Coupé, the aluminum fraction comprises 63 kilograms (138.89 lb) of panels, 45 kilograms (99.21 lb) of castings and 32 kilograms (70.55 lb) of extruded sections.
The ASF body of the Audi TT is the ideal solution for a sports car. Compared to the preceding model, static torsional rigidity increased by 50 percent in the Coupé and 100 percent in the Roadster. This lays the foundation for precise, dynamic handling, while also being responsible for the high vibrational comfort and superior crash safety. In 2006 Audi won the Euro Car Body Award, the world’s most important prize for innovative car body design, for the ASF body of the TT.
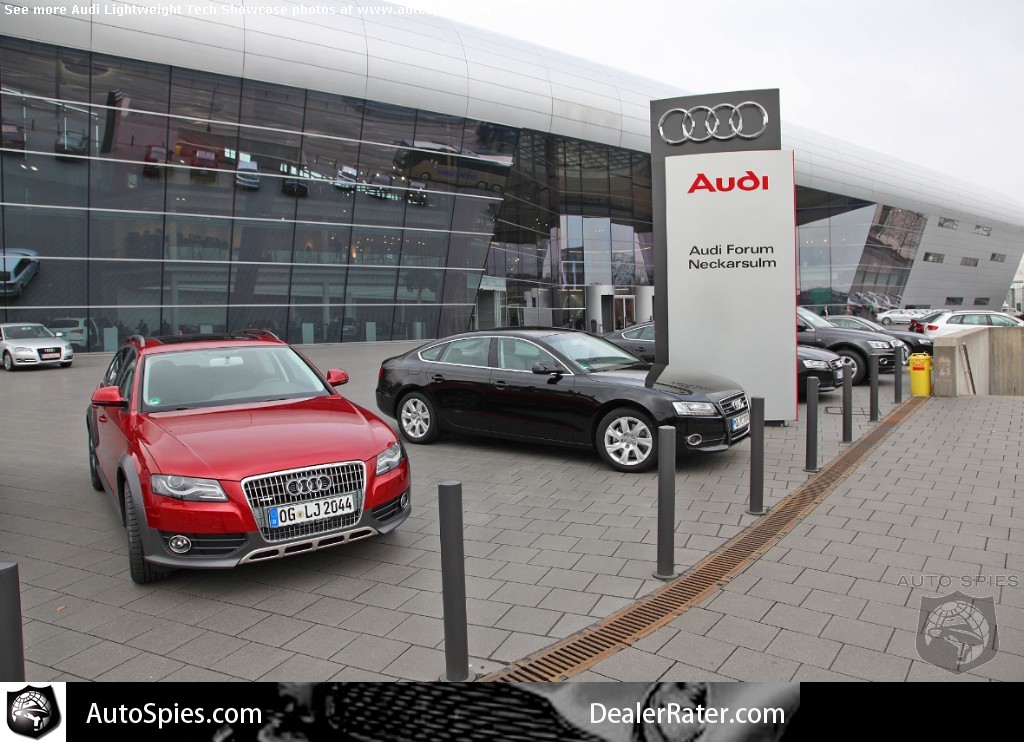
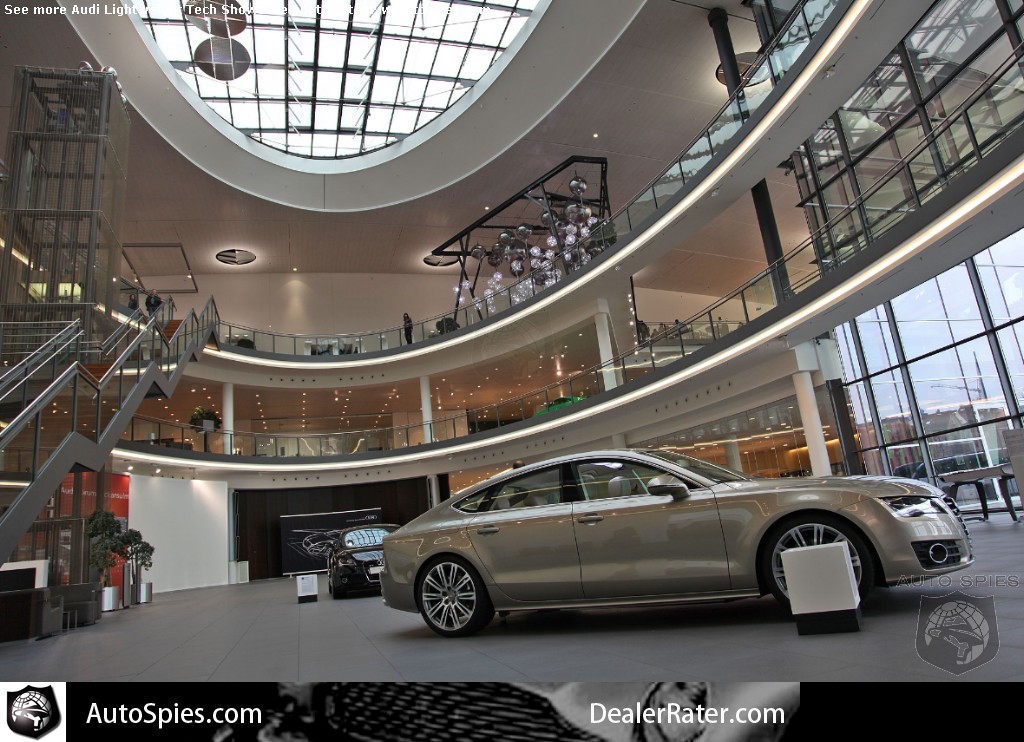

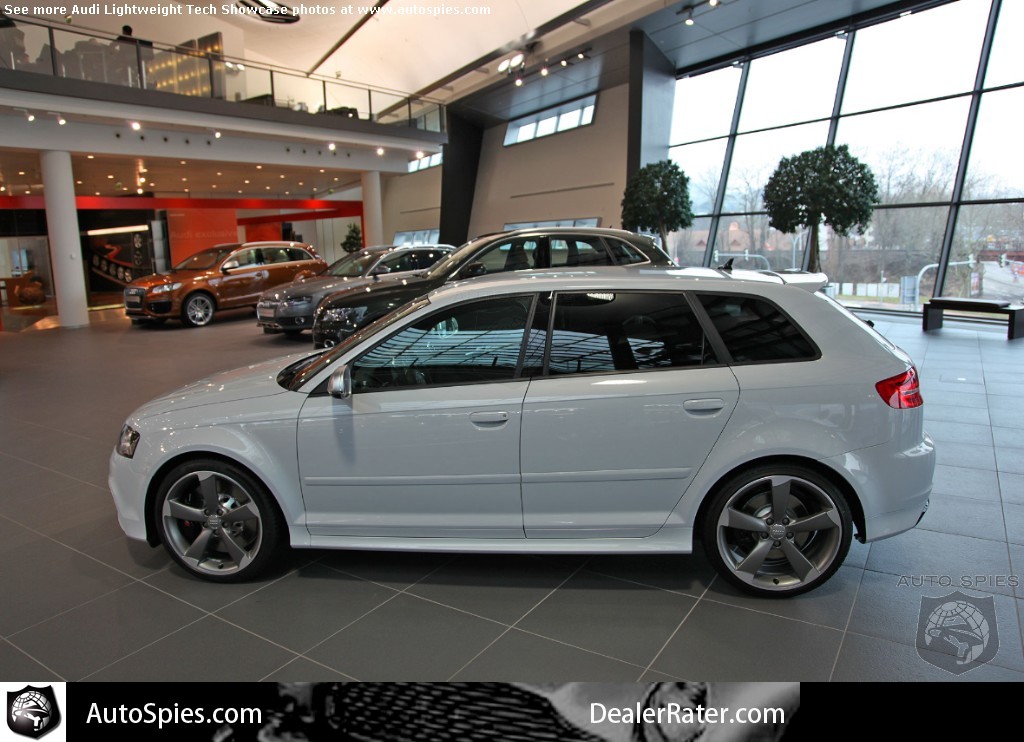
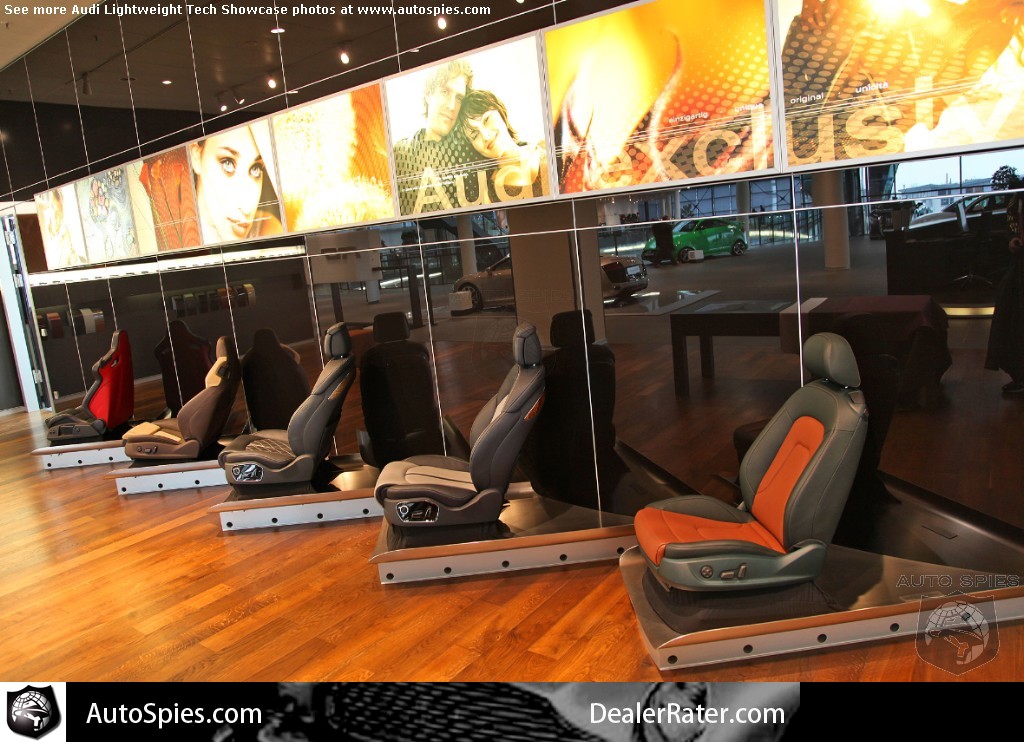
The Audi R8 (2007)
The ASF body of the R8 set new standards. The body is unmatched in the high-performance sports car segment in terms of lightweight quality – the relationship between size, weight and rigidity.
Weighing 210 kilograms (462.97 lb), the superstructure of the R8 Coupé makes extensive use of extruded sections, which account for 70 percent of the total. Vacuum-cast nodes account for 8 percent, and aluminum panels make up the remaining 22 percent. A magnesium engine frame provides added rigidity in the upper section of the rear end. Custom tailored blanks reinforce the center tunnel. The individual panels vary in thickness depending on where they are used.
Plastic is used for the R8’s front fenders and the sill liners. The hood of the Coupé is made of composite materials; the side blades are optionally available in carbon fiber-reinforced plastic (CFRP).
In the R8 Spyder (body weight: 216 kilograms (476.20 lb)), profiles dominate the mix even more clearly than in the Coupé, accounting for 75 percent. The structure of the open high-performance sports car integrates the rear side walls and the cover of the storage compartment for the top as load-bearing CFRP components.
Audi reduced the weight of the exclusive, top-of-the-line R8 GT by 100 kilograms (220.46 lb) to 1,525 kilograms (3,362.05 lb). Made of CFRP, the rear trunk lid, the back bumper and the side blades account for 13.3 kilograms (29.32 lb) of this; the thin aluminum cover over the luggage compartment is good for an addition 2.6 kilograms (5.73 lb). Glazings of thinner glass or polycarbonate shave off nine kilograms (19.84 lb).
In the passenger compartment, lightweight carpeting and a seat frame of glass-fiber-reinforced plastic reduce the weight by 7.9 and 31.5 kilograms (17.42 and 69.45 lb), respectively.
The Audi A8 (2010)
The third generation of the A8 once again features great advancements in the ASF principle. The material mix of the body, comprised of 251 individual parts, includes 13 different grades of aluminum. The superstructure also integrates ultra-high-strength B-pillars of hot-shaped steel – a groundbreaking step. The body of the sedan with the standard wheelbase weighs just 231 kilograms (509.27 lb); 10 kilograms (22.05 lb) more in the A8 L.
Besides the steel B-pillars, which account for 8 percent of the weight, aluminum castings and panels each account for 35 percent and extruded sections for 22 percent. The combined weight of the 25 castings, most of which are made of advanced alloys, is three kilograms (6.61 lb) less than with the previous model. Most of them are manufactured using the very high-precision vacuum casting process.
Audi has increased the strength of the higher-strength body components by as much as 25 percent, thereby reducing both material thickness and weight by up to 20 percent. The fusion alloy for the aluminum panels alone saves 6.5 kilograms (14.33 lb) of weight. Fifteen fusion panels are used for the load-bearing parts of the structure. The Euro Car Body Award that Audi received in late 2010 documents the innovation density of the A8 body.
The Audi A6 (2011)
The bodies of the new Audi A6 and the A7 Sportback are also best-in-class. A hybrid steel-aluminum construction, they weigh roughly 15 percent less than a comparable all-steel body. They are made up of more than 20 percent aluminum, making them roughly 30 kilograms (66.14 lb) lighter than that of the previous A6 model.
The hybrid concept, in which the aluminum components are largely concentrated in the front end, improves the axle load distribution. Most importantly, though, it provides the basis for systematic lightweight construction. Depending on the version, the A6 weighs as much as 80 kilograms (176.37 lb) less than its predecessor. Audi has reversed the weight spiral yet again.
The crossbar in the engine compartment and the cross-members behind the front and rear bumpers are aluminum sections. The front strut domes are aluminum castings. The integral subframe behind the instrument panel, the rear shelf, the bulkhead to the trunk, the cross-member in the trunk, the front fenders, the doors, the hood and the trunk lid are made of aluminum panels. A new pretreatment process ensures that the steel and aluminum components can be painted in exactly the same way.
The passenger compartment of both the A6 and the A7 Sportback includes components made of hot-shaped steel. They can be found in the transition from the front section of the car to the passenger cell, in the A-pillars and the roof arch, as reinforcements for the center tunnel and the side sills, at the transition of the side sills to the rear section of the car, as cross-bracings in the floor panel and as B-pillars. In many zones, such as the bulkhead cross-connection, Audi uses tailored blanks. These are sheets of different thicknesses that have been rolled in some cases to different thicknesses.
In some areas, the steel components in the body already follow the ASF principle. The A6 and the A7 Sportback represent the gradual transition from the monocoque design to the new Multimaterial Space Frame (see separate section).
Experience lightweight construction – test cars at Tech Day
The customer benefits directly from Audi’s lightweight construction – it makes the cars more efficient and more dynamic. These strengths can be experienced first hand in drives on the test track and on public highways at Tech Day.
Test 1: Audi A6 comparison
Two Audi A6 3.0 TDI quattro models – the outgoing model and the new successor model in a comparison test. Thanks to the systematic lightweight construction concept, the new sedan weighs up to 80 kilograms (176.37 lb) less than the predecessor model. The difference is clearly noticeable while driving. The new A6 seems a decisive tick sportier, more spontaneous and more agile in all criteria.
Test 2: Test drive with weight-optimized Audi TT
An Audi TTS Coupé model with a range of weight-optimizing measured acts as a technology platform which is already geared toward the next generation of the model series. The 2.0 TFSI produces 200 kW (272 hp) as standard and delivers its power to the quattro drivetrain via a six-speed S tronic transmission.
With its hybrid body, the production model of the TTS is already unusually light with a curb weight of only 1,470 kilograms (3,240.80 lb). In the prototype, add-on parts of carbon fiber-reinforced plastic, in particular the special lightweight seats and other individual components, save another 80 kilograms (220.46 lb), an effect that is most noticeable in the increased lateral dynamics. Special features can also be found in the passenger compartment. The driving modes of the S tronic on the prototype are selected using buttons. The rings of the scales in the instrument cluster are illuminated in white in D mode, red in the sporty S mode.
Test 3: Driving experience with the technology of the Audi quattro concept showcar
An especially attractive technology platform can be experienced in the form of an Audi A5. The lightweight 2.5 TFSI 5-cylinder turbocharged engine with 300 kW (408 hp), familiar from the quattro concept showcar, accelerates the test vehicle. The body of the is hand-built from aluminum components according to the ASF principle. Add-on parts such as the hood and the rear hatch are made of a carbon fiber composite material. Lightweight sport seats are installed up front. This one-off model weighs just 1,400 kilograms (3,086.47 lb). Its power-to-weight ratio is 3.4 kilograms (8.16 lb) per hp, better than even that of the Audi RS 5, whose 4.2-liter V8 produces 331 kW (450 hp). The technology platform’s performance is awesome, when accelerating, when braking and especially when cornering.
The Audi quattro concept, of which a 1:4 scale model will be on display at Tech Day, is the ideal successor to the Audi Sport quattro from 1984. This is true for the compact length of 4.28 meters (14.04 ft), for the powerplant – a five-cylinder turbo with 300 kW (408 hp) – and for the low weight of around 1,300 kilograms (2,866.01 lb). Each hp only has to move 3.2 kilograms (7.05 lb) of weight, leading to exhilarating performance. The quattro concept catapults from 0 to 100 km/h (62.14 mph) in just 3.9 seconds.
Unlike the 1980s classic, the Audi quattro concept has a body of aluminum. This is assembled in typical ASF fashion from extruded sections, pressure diecast components and aluminum panels. The bodyshell weighs only 159 kilograms (350.53 lb), around 40 percent less than a comparable body made of steel sheet. The hood, the rear hatch and the moveable spoiler are made of a carbon fiber-reinforced composite.
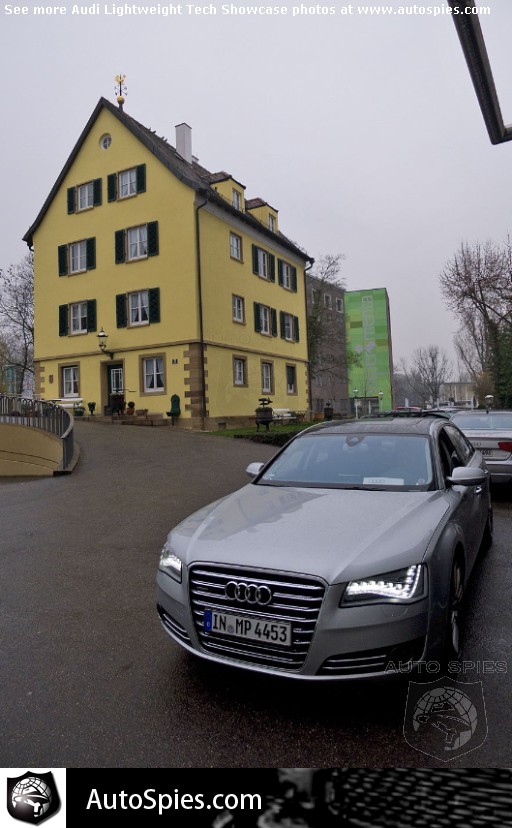
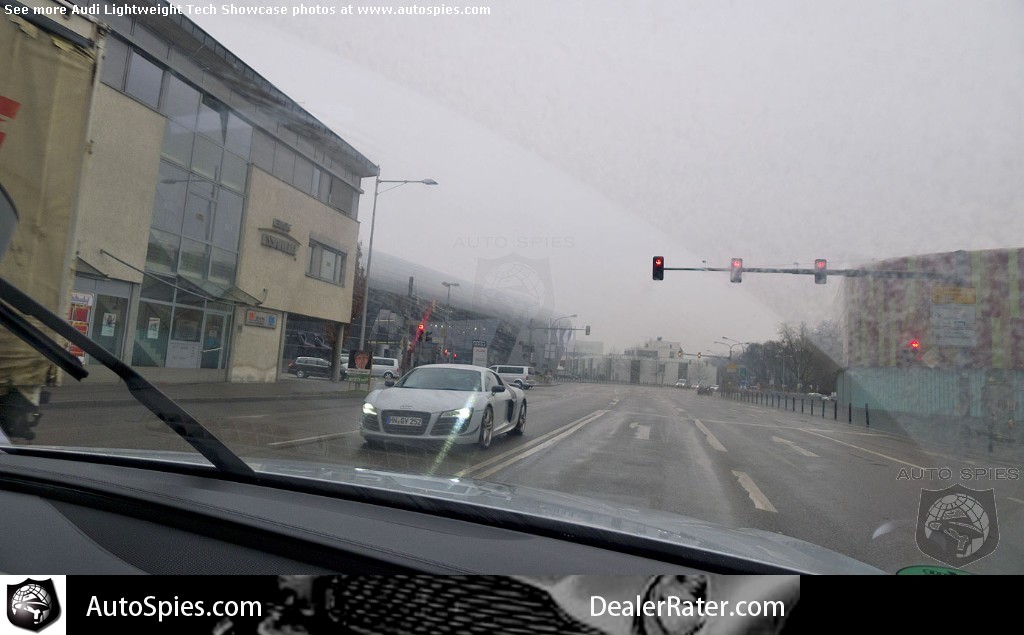
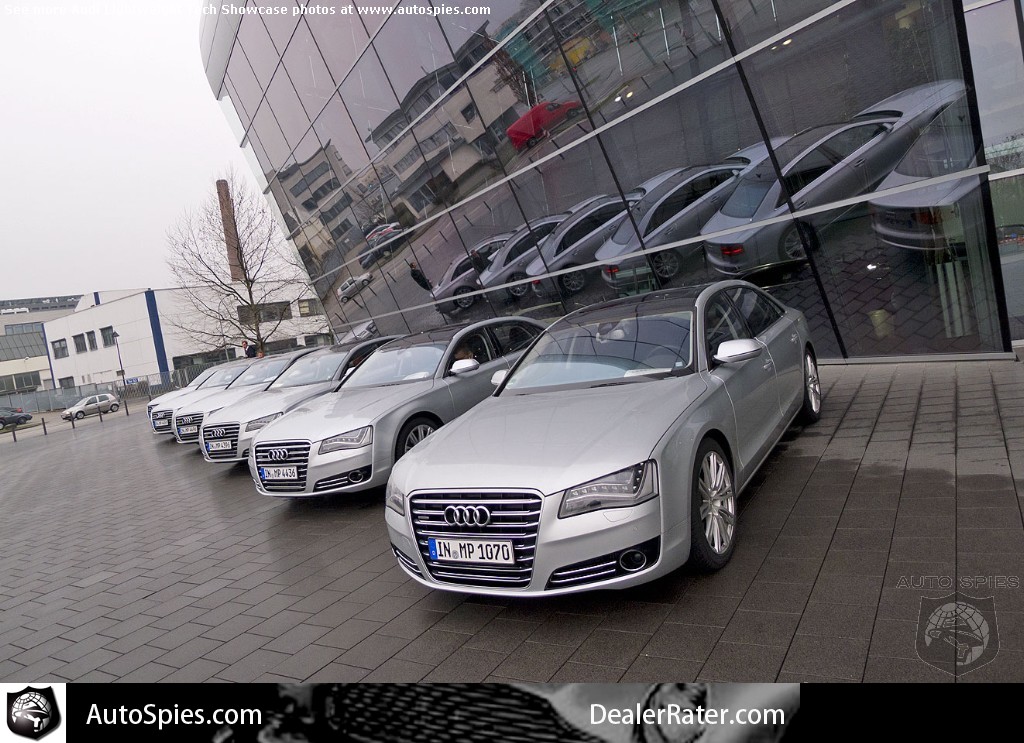
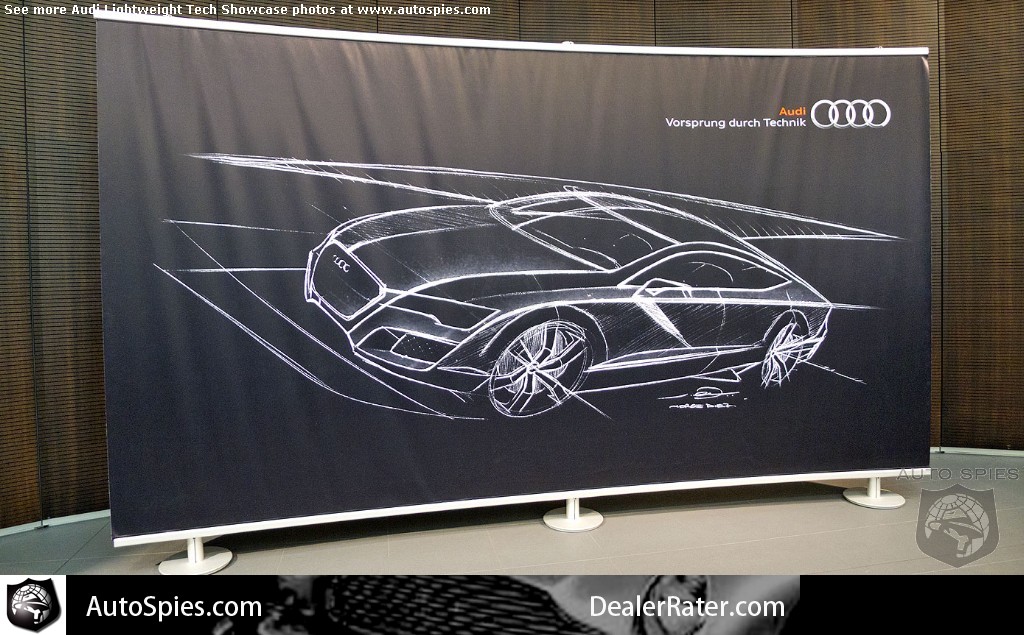
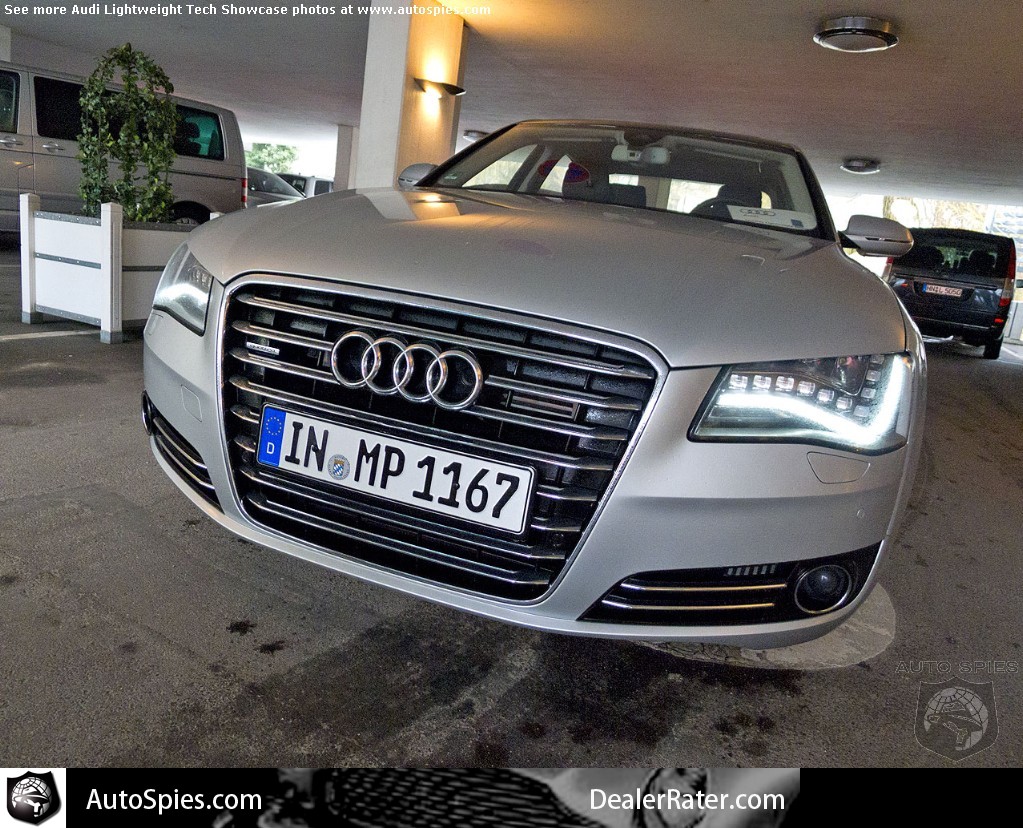

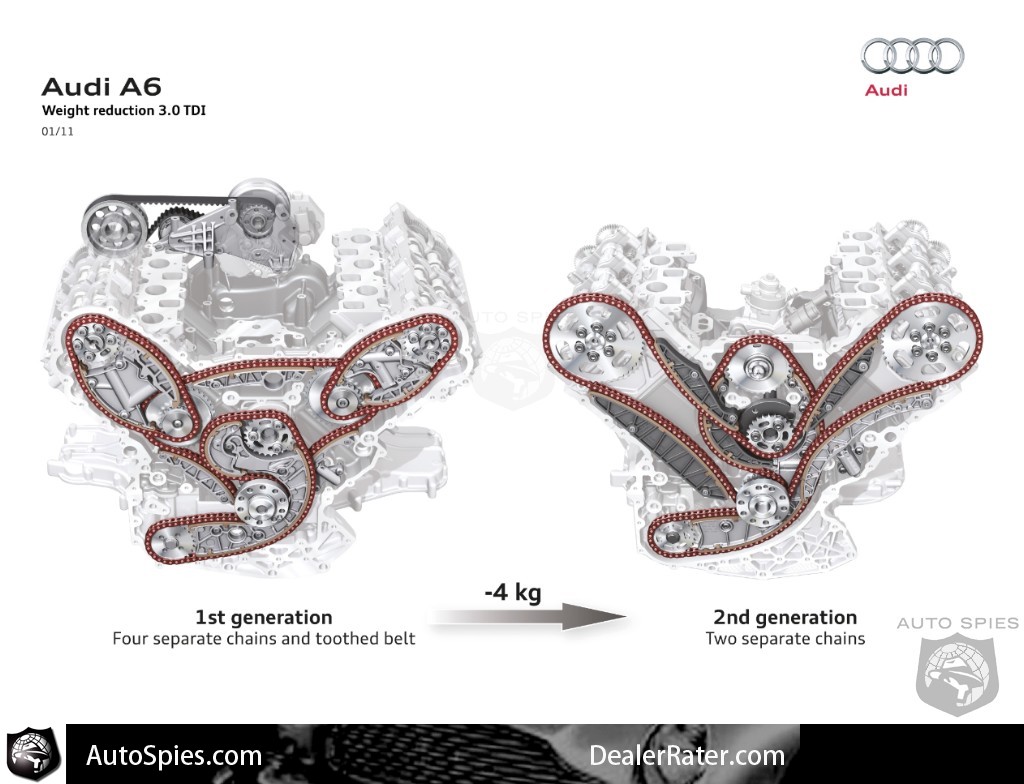
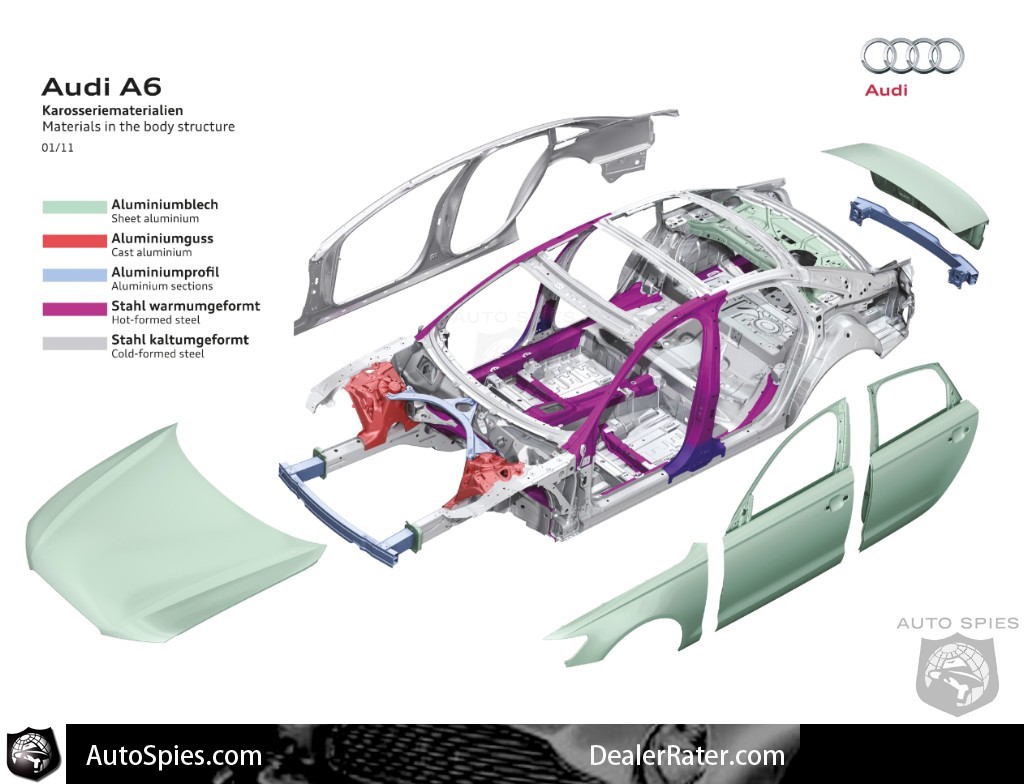
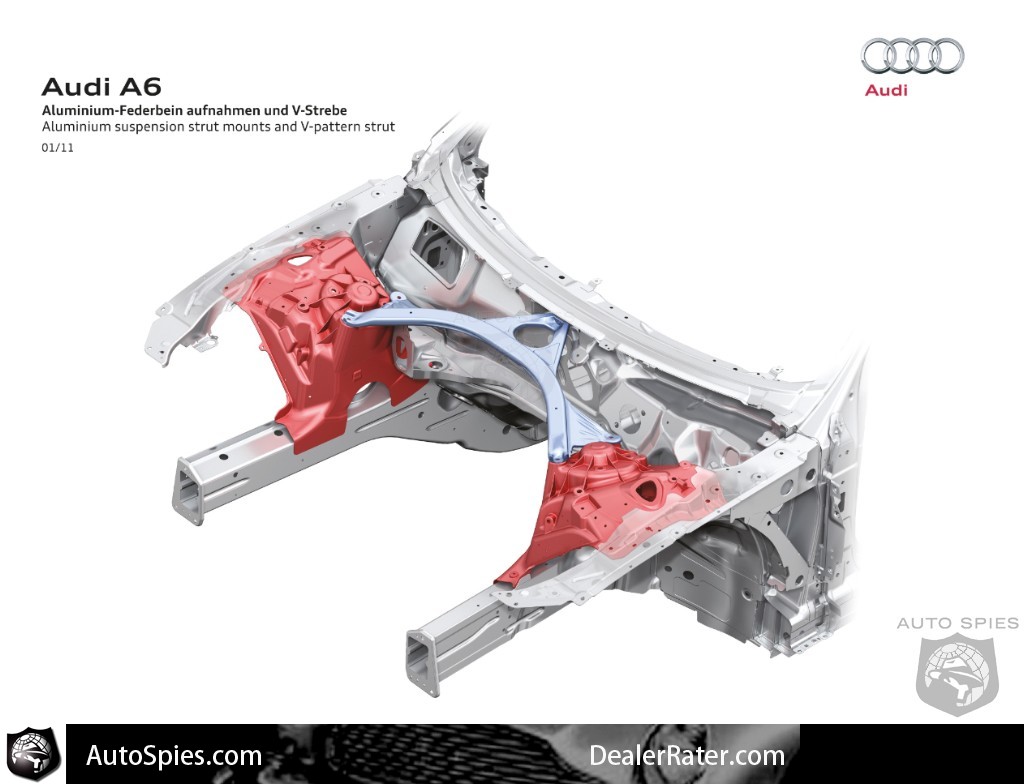
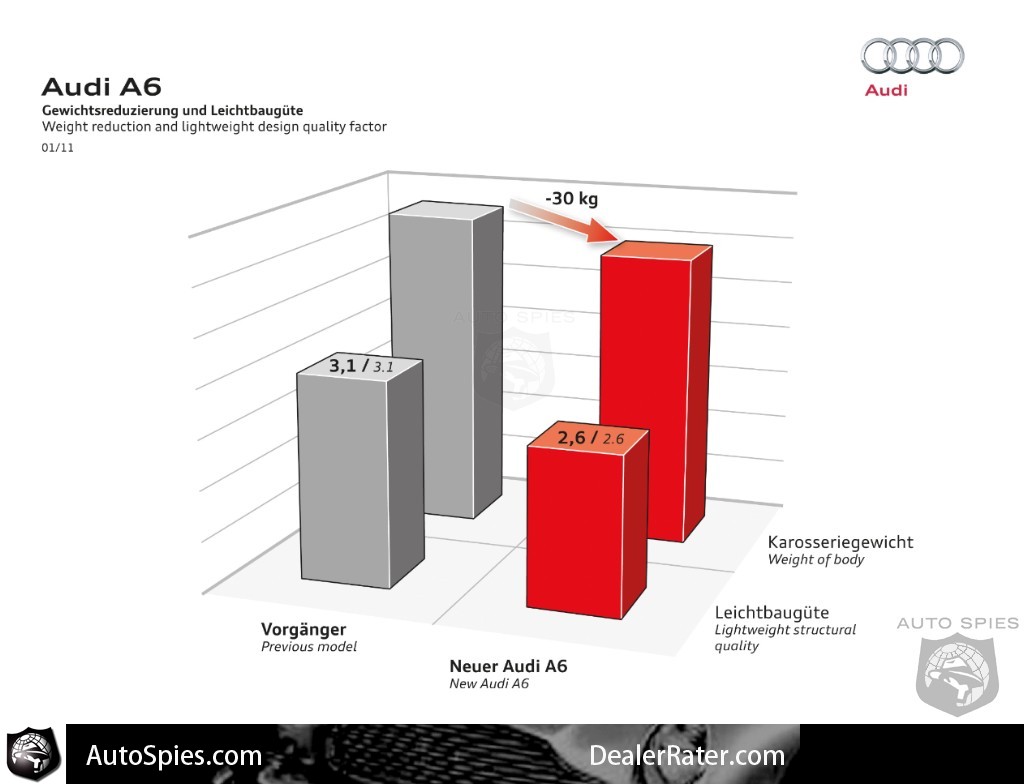
Audi Lightweight Tech Showcase Photo Gallery
2011 Geneva Motor Show Preview Photo Gallery
2012 Mercedes-Benz C-Class Coupe Photo Gallery
2012 Audi A6 Launch Photo Gallery
Porsche 911 Experience Photo Gallery