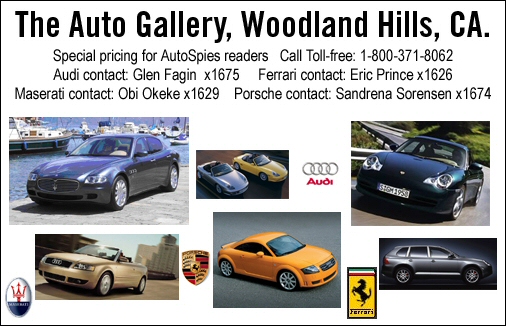
Mercedes-Benz A-Class: saving equivalent to 1,300 litres of petrol per vehicle
The new A-Class that was premiered on September 10, 2004 is not only setting new standards in terms of safety, comfort, high-quality feel and dynamic handling but also in terms of environmental protection.
The development of the compact car was based around an integrated environmental concept which covers the vehicle’s entire lifecycle. Over 40,000 individual processes were analysed and optimised from an environmental standpoint. As a result, emissions have been reduced in the manufacture and use of the new A-Class by up to 17 per cent compared with the outgoing model.
Energy consumption drops by around eight per cent – this equates to a saving of around 1300 litres of petrol per vehicle. Environment-friendly product development has also led to the increased use of recycling-friendly plastics and natural materials. Around 21 per cent of all plastic components are produced from high-quality recycled plastics – three times higher than for the outgoing A-Class. 26 components of the latest Mercedes model are made from renewable raw materials.
A combination of technological innovations in the body, chassis and engine design and advances in manufacturing processes allow Mercedes-Benz to reduce the emissions generated through the production and use of the new A-Class. Examples of these successful developments include the solvent-free powder clearcoat, which protects the body, and the new or modified petrol engines. Despite their higher output, these power units consume up to ten per cent less fuel and meet the stringent EU 4 exhaust emission limits.
With its far-sighed selection of materials, Mercedes-Benz is likewise making a crucial contribution to preserving resources and lowering the levels of emissions which can be produced through the material recycling process for cars after they have reached the end of a long service life.
Experts in the environment-friendly product development department at the Mercedes-Benz Technology Centre (MTC) have compiled an impressive pool of knowledge as part of an environment-oriented assessment programme carried out over the full course of the A-Class’s service life:
Emissions of the greenhouse gas carbon dioxide produced in the manufacture of the new A-Class and by its use over a full lifecycle will be around nine per cent below the levels of the outgoing model.
Primary energy consumption has been reduced by roughly the same degree, falling around 50 gigajoules below the value of the outgoing A-Class. This equates to the energy stored in some 1,300 litres of petrol.
With the new A-Class, Mercedes-Benz has also made remarkable progress in reducing emissions levels compared with the outgoing A-Class in terms of other pollutants such as:
Nitrogen oxides: down 17 per cent
Sulphur dioxide: down 6 per cent
Volatile hydrocarbons: down 8 per cent
Special waste materials: down 10 per cent
The Mercedes experts have looked at over 40,000 individual processes as part of their integrated environment analysis for the new A-Class. The overall assessment covers a total of more than 200 “input” factors (resources) and some 300 “output” parameters (emissions).
Share of approved recycled components more than three times higher
The Mercedes “Design for Environment” philosophy begins with the selection of materials. Only materials boasting low consumption of resources, outstanding recycling properties, a minimal energy requirement and low emissions in their manufacturing, processing and use are permitted in the construction of the Stuttgart-based brand's passenger cars. On this basis, the new A-Class already satisfies the recycling rate of 85 per cent stipulated Europe-wide from 2006 and is also set to meet the recycling target of 95 per cent – with a maximum of ten per cent of the car parts being allowed to be utilised for incineration to produce energy - planned for implementation in 2015.
The new Mercedes compact car consists largely of materials for which recycling processes have already been developed and tested:
Steel and iron-based materials: 65 per cent
Plastics: 17 per cent
Non-ferrous metals and light alloys: 7 per cent
When it comes to preserving resources, Mercedes-Benz gives high-quality secondary raw materials priority wherever possible. Mercedes experts have had some positive experiences with the use of recycled plastics and are committed to channelling plastics from end-of-life vehicles and scrapped car parts back into the production of new vehicles. A total of 54 components with a combined weight of 34 kilograms are made from high-quality recycled plastics – equating to 21 per cent of all the plastic parts used. The number of approved recycled components for the new car is therefore more than three times higher than was the case for the outgoing model.
26 components made from natural materials
The development and production of car parts made from renewable raw materials is another important part of preserving resources and of the Mercedes “Design for Environment” philosophy. Mercedes-Benz sees the use of natural materials as an important contribution to reducing carbon dioxide emissions. After all, using renewable raw materials helps to put the brakes on the consumption of traditional energy resources such as coal, natural gas and petroleum.
In the new A-Class, 26 components with a combined weight of 23 kilograms have been manufactured using natural materials. The combined weight of components made from renewable raw materials has therefore risen by around 98 per cent from the levels in the outgoing model. One example of the use of natural materials in automotive construction is the covers for the front seat backrests in the new A-Class, which consist of a combination of plastic and flax fibres.
And Mercedes engineers have also opted for a natural raw material to ensure fuel tank venting, with olive wood used in the production of an activated charcoal filter. This microporous material absorbs the hydrocarbon emissions and is self-regenerating.
The latest tests carried out as part of DaimlerChrysler’s materials research show that natural fibres are also extremely effective in material composites. Indeed, they could even replace glass fibre as a strengthening agent in plastic parts for car bodies thanks to their exceptional bending and tensile strength. Natural fibres also stand out from glass fibres with their lower weight, superior ease of use and suitability for recycling. Another source of natural materials is the abaca plant, which grows in the Philippines. Its fibres, which are extremely elastic and boast impressive tensile strength, are currently being tested for use in the manufacture of part of the underfloor panelling of the new A-Class. Abaca fibres are considered to be the strongest and longest natural fibres on the planet.