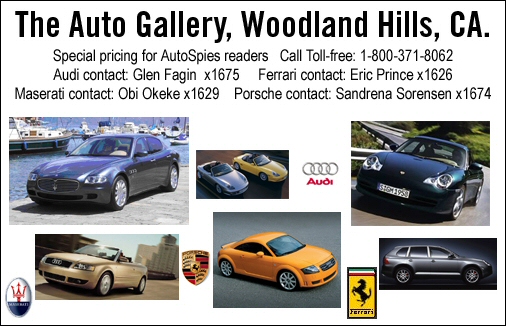
A Prize-Candidate Laser Process at Audi, and its Inventors
Light at the end of the cylinder
• Machining of cylinder bores reduces engine oil consumption by up to 75 percent
• Wear to the bores and piston rings reduced by as much as 90 percent
• Nomination for the German Future Prize
as a reward for years of research work
Horst Lindner is a striking phenomenon: tall and powerful. This 62-year-old exudes self-confidence. Most of all when it comes to his work. Then he becomes a committed storyteller. He talks about atomic bonds, nanocrystalline structures, superplasticity, laser pulses, tribology and microns just like others speak of the weather or the football results. Lindner, responsible at AUDI AG for the development of production processes, is currently talking most of all about a prize-candidate machining process in engine production: "Exposure of the cylinder bores of internal combustion engines to UV laser light" It sounds thoroughly scientific and complex, and it really is. He and two other co-researchers have now been nominated for the "German Future Prize 2004" – the German President's prize for technology and innovation – on the basis of the project. Because the findings from the microscopically small world of Horst Lindner are delivering major benefits in terms of motoring ecology and economy.
He is not the only "shining light" in the UV laser process project group. Along with him, the physicist Robert Queitsch of the ATZ Development Centre for Process Engineering and the recently deceased Prof. Hans W. Bergmann of the Chair of Metallic Materials at the University of Bayreuth have also been nominated for the German Future Prize.
In fact the laser process is throwing a lot of light on the darkness that surrounds the grey cast iron engine block. Machining the surface of the cylinder bores with the beam of ultra-violet light reduces engine oil consumption by up to 75 %, and wear to the cylinder bores and piston rings by as much as 90 %. And there was something else that made the work of the three researchers worthy of nomination by the independent jury of the German Future Prize. It is already beyond the research stage, and has been in use for series production at Audi's Hungarian plant in Györ since January 2004. The 3.0 TDI diesel engines that are already being installed in the Audi A6 and the Audi A8, and that will shortly also be supplementing the range of engine options for the VW Phaeton and the VW Touareg, are produced there using this machining process. So both the environment and the customer are already benefiting from this useful surface treatment.
But how does such a microscopically small cause have such a major effect? Let's take a stroll through the world of microns and motors with Horst Lindner and Robert Queitsch.
"In internal combustion engines," says Lindner, explaining the basic principles, "the chemical energy of the fuel is converted into mechanical power to drive a vehicle at the very heart of an engine, in the cylinders. The surface of the cylinders (cylinder bore) serves as the sliding surface for the piston rings and the piston itself. Furthermore, the system made up of the cylinder bore and the piston rings is what forms the seal between the combustion chamber and the sump. The surface topography of the cylinder bore has a crucial influence on the engine's oil consumption, and hence on emissions."
One primary development objective with internal combustion engines is of course, says Lindner, to reduce fuel consumption. This also requires higher compression. Associated with this, however, there is also increased mechanical load on the cylinder bore/piston rings system. "The cylinder bore must therefore be designed in such a way that it can cope with higher tribological demands (friction, wear) along with lower oil consumption."
A process known as honing has been used worldwide to date to machine these cylinder bores. This honing is carried out using a cylindrical tool fitted with abrasive elements. The circular movements of the tool create a crisscross scored structure on the cylinder bore, in which the oil can be retained. The scored structure does indeed retain a considerable volume of oil, but there are limits to the reduction in oil consumption. Lindner adds: "High oil consumption also means a high proportion of unburned hydrocarbons in the exhaust, along with a reduction in the effectiveness of the NOX catalytic converter located in the exhaust gas flow, as a result of the sulphur content of the oil additives or of basic oil itself."
But that is not the only imponderable in the conventional machining process. Lindner: "In addition to the crisscross scored structure, a honed surface is characterised by warping and displacement of material, known as "metal coating formation". The "metal coating" created when honing really clogs the graphite releases coming to the surface in the grey cast iron. As a result they are not available to retain oil."
Laser expert and graduate physicist Robert Queitsch contrasts with this the advantages of the new process: "UV laser exposure for the machining of grey cast iron cylinder bores is fundamentally different from the honing process. UV exposure is carried out over the entire area throughout the sweep of the piston ring.
When the UV laser pulses hit the surface of the cylinder bore, which has been pre-machined to a minimal roughness by honing, material is vaporised and the graphite releases are opened up. Queitsch explains that in this way a micro-hydrodynamic surface structure is formed, which serves to retain oil. That means that oil can collect more easily in the microscopically small "hollows" that are created in this way. At the same time the surface is melted in place by the laser down to a thickness of one to two microns (that is one or two thousandths of a millimetre). "A vaporized metal plasma is created in the process. Plasmas are vapours or gases containing tremendous energy. This energy produces intense extending pressure, by means of which 16 to 18 % nitrogen is impregnated into the melted layer.
This leads to the instantaneous solidifying of the thin melted layer as soon as the laser pulse ends, and hence to a nanocrystalline structure. "The high nitrogen content and the nanocrystalline structure permanently improve the resistance of the cylinder bore to wear and corrosion, and the material also gains ceramic characteristics as a result of the high nitrogen content," explains Lindner.
When the engine is running the solidified nanocrystalline structure is transformed by the heat of combustion and friction in the peripheral area (approx. 150 to 200 nanometres) into an extremely fine structure of iron crystals with carbon and nitrogen. Lindner: "Structures of this type have superplastic properties. That means that the release of atoms from the atomic bond is inhibited by its ability to give. This results in increased resistance to wear. This self-conditioning effect is a tribological revolution!"
With the cylinder bore exposed to the UV laser, the scientists were able to demonstrate a reduction in wear to the cylinder bore and piston rings of up to 90 %, depending on the operating condition of the engine, when compared with a conventionally well honed cylinder bore. "And reduced wear also means reduced loss of performance resulting from friction within the engine, and hence fuel savings," says Lindner.
Oil consumption measurements in a comparison with the conventional honed surface produced the following results: With conventional honing the oil consumption amounted to between 20 and 50 grammes per hour over a running period of 800 hours, with significant initial oil consumption, and rising after a period of 400 hours. In the case of the UV laser-exposed cylinder bore, stable oil consumption of 9 grammes per hour was recorded over a period of 820 hours, and the initial oil consumption familiar with honing did not arise.
A large number of car and commercial vehicle manufacturers are now showing a lot of interest in the patented UV laser exposure of cylinder bores, along with suppliers from throughout Europe.
But Lindner and Queitsch see even more potential for the technology: "We see possible applications for mechanical components in general made of grey cast iron, and for steel materials that are exposed to tribological loads and are hence subject to wear. Friction and wear are matters of economics. Wear means loss of use of machines, and the cost of maintenance and repair work. Estimates of friction and wear-related costs in Germany lie between two and seven percent of GDP (EUR 2,129 billion). Assuming a mean value of 4.5 %, this means costs amounting to EUR 95.8 billion," calculates Lindner.
Nomination for the German Future Prize is for Horst Lindner and Robert Queitsch the reward for their many years of research work. A reward that Professor Hans W. Bergmann, as co-initiator of the project, can no longer pocket. He passed away in the year 2000.
The researchers started their first serious experiments as long ago as 1990. In those days it was with a laser donated to them by Siemens. A minor anecdote in passing: This high-tech installation was actually intended for use in the planned atomic reprocessing plant at Wackersdorf (WAA), for separating the isotopes that would have been necessary for the recovery of nuclear fuel rods. As is well known, this all came to nothing when the WAA project was shelved in 1989. The laser, on the other hand, laid the foundations for the development of this innovative technology.
This is already the second nomination of Audi employees for the German Future Prize. In 2002 the Ingolstadt car manufacturer was similarly in the top four in the context of a cooperative project. On that occasion it was for an optoelectronic processor, enabling a vehicle to "see" in three dimensions.
In The UV Laser Plant in Györ
May 2003 a start was made at AUDI HUNGARIA MOTOR Kft. in the Hungarian city of Györ on the construction of the UV laser plant. The fully automated plant, consisting of two parallel units, has been running since January 2004 on the series production of the 3.0 TDI diesel engine. Maximum throughput capacity is designed to be 700 engines per day. Each grey cast iron engine block is rotated on a turntable at 120 rpm around the laser head. The cycle time for a complete engine block including handling is just 184 seconds, and the exposure time for each cylinder bore is 20 seconds. In comparison: Under laboratory conditions at the start of the project the researchers took around three hours to machine a cylinder block with the laser. Audi has invested EUR 4.8 million in the 4.60 metre long, 7.60 metre wide and 3.50 metre high plant, which is completely enclosed by a steel chamber. It is operated by one employee per shift, who has undertaken training in laser technology in addition to his/her basic qualification as a skilled technician. There are altogether around 250 staff employed in Györ on production of the 3.0 TDI engines.
The "German Future Prize"
The German Future Prize – a prize for technology and innovation – is awarded once a year by the German President. This is a prize originated by the Head of State, so it is not just a matter of patronage. The renowned prize was awarded for the first time in 1997. Its initiator was the then President of Germany, Roman Herzog. The German Future Prize is endowed with EUR 250,000 and is awarded in a national competition in recognition of outstanding technical, engineering or scientific innovation. It is also intended to promote a technology and innovation-friendly climate in Germany. Application to be considered for the prize is excluded. The candidates are nominated by a jury made up of independent experts from industry and the academic world. Following on from Roman Herzog and Johannes Rau, this year Horst Köhler will be the third President of Germany to award the Future Prize. The award ceremony will take place in Berlin, on 11th November. This is already the second nomination for Audi employees.
Future Prize 2002: Sensor for the "Seeing Car"
This is the second time that Audi employees with an innovative project have been nominated for the German Future Prize. The last time that the Ingolstadt car manufacturer was at the forefront of innovation in Germany was in 2002, on that occasion in the context of a joint venture for the development of an image sensor enabling "three-dimensional" vision.
Mechanical vision, and "understanding" what is seen, had up to that point only been possible with sophisticated stereo cameras along with a large-scale computing power. With the optoelectronic processor, developed by Prof. Dr. Rudolf Schwarte of the University of Siegen, the complex procedure of seeing and understanding in three dimensions can be simplified and hence made more affordable. This sensor essentially consists of a "Seeing Diode", which can immediately determine the distance between an object and the diode by means of reflected infrared radiation.
There is a wide range of possible applications. Mechanical vision enables for example the detection of vehicles in the blind spot. It also means the driver can be warned in good time if he/she runs the risk of leaving the carriageway. Another area of application is smart control of the airbag. The sitting position of the passengers can be determined before the airbag is triggered. The airbags are then filled accordingly to achieve the optimum protective effect. Initial series production development is already set to start in the coming year. There is, however, also potential for the technology of three-dimensional vision inside the car, such as in the area of virtual reality or in games consoles.
The others nominated in addition to Prof. Schwarte were the two managing directors of PMDTechnologies GmbH (Siegen), Dr. Bernd Buxbaum and Torsten Gollewski (Audi Electronics Venture). PMDTechnologies is a joint venture between Prof. Schwarte and Audi Electronics Venture GmbH, a wholly owned subsidiary of AUDI AG. The innovation cycles for electronics are becoming increasingly shorter. In this environment, Audi Electronics Venture provides an enterprise concept enabling market access for innovations by small, high-tech companies, particularly to the automotive market.
Glossary: From Honing to Tribology
• Honing is a way of machining metal surfaces by removing extremely fine slivers. This method is particularly widely used for the interior surfaces of bores and the exterior surfaces of shafts. Precision when honing is measured in m).microns (
• m (= 1/1000 mm).Micron: A unit of length with the abbreviation
• Nanocrystalline structure: The size of the crystals in a crystalline material lies in the nanometre range for a nanocrystalline structure. Nanocrystalline materials are harder and very resilient, they are less sensitive to fatigue fractures than conventional metals, which have crystal sizes in the micron range (1 micron – 1000 nanometres).
• Nanometre: A unit of length with the abbreviation nm (= 1 billionth of a metre) A nanometre corresponds to approximately five iron atoms placed one on top of another.
• Tribology: Tribology is a science that deals with way surfaces moving in relation to one another are affected. It includes the topic areas of friction, wear and lubrication, both between two solids and between solids and liquids or gases.
• Topography: The term topography comes from Greek, and means description of location. Topography is primarily concerned with the description of landforms in the originally geographical sense, and in its narrower sense topography also means the terrain itself. Here the term is to be understood in the context of the observation of microscopically fine surfaces in the fields of metallurgy and materials testing.
• Vaporised metal plasma When vapour is created in the machining of metal, this vaporized metal absorbs more and more energy and heats up as a result. The degree of ionisation rises as a result of this, and vaporized metal plasma is formed.
• Superplasticity: Extraordinarily high ductility of polycrystalline materials.
• Laser pulse: In a laser pulse there is no uninterrupted beam of light emitted, just short flashes of light. Higher power per flash is possible in pulse mode than in continuous mode.
• Grey cast iron: Cast iron with a light to dark grey fracture surface. This is a result of the release of carbon in the form of graphite.