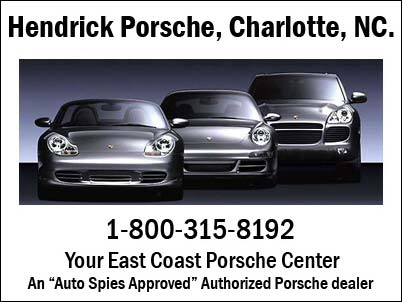
VIRTUAL REVOLUTION AT VOLKSWAGEN
3D technology sets standards in vehicle development
Volkswagen invests 20 million euro in new visualization centres
WOLFSBURG, Germany - Turn the steering wheel, adjust the interior mirror, look at how the light and shadow falls on the surface of the vehicle, even see reflections of the body in the rearview mirrors - from now on, Volkswagen engineers and designers can do all this in virtual three-dimensional space without touching a single piece of metal.
New 3D technology is revolutionizing vehicle development at Volkswagen and setting standards in the automotive industry: using real-time "Ray Tracing”, 3D objects are displayed, moved and modified instantly and interactively. Thanks to powerful computer technology, large and complex volumes of data can now be processed. Even realistic shadows, refractions of light and reflections can be generated. Real-time "Ray Tracing” was chiefly developed by Professor Dr.-Ing. Philipp Slusallek of Saarbrücken University and is making its world industrial debut at Volkswagen.
Two unique visualization centres have been built within Technical Development at a cost of around 20 million euro. Here, developers, designers and engineers from all departments will work together, thereby making the vehicle development process more efficient and reducing cost and time expenditure considerably. Engineers can get a realistic and detailed impression of a planned vehicle in the early stages of development on large projection screens.
A special projection screen, the so-called "Powerwall” (5.10 m x 2.10 m), enables designers or test engineers to display life-sized vehicles. Preliminary virtual designs are produced at short-notice and cost-effectively to be viewed and discussed: reflections, curves or paintjobs can be assessed on these virtual models just the same as on a real vehicle. The highlight of the technology: in the direct comparison between "actual” and "target”, cameras pick up images from a real development vehicle ("actual state”) which are then compared with the virtual images ("target state”) on the "Powerwall”. Any differences are then measured and immediately incorporated into the modification process before components are produced.
Another key element of the project visualization centre is the "Cave”, a cube with a side length of 2.35 metres. An image is projected onto each of its screens from outside - as in a 3D cinema. Inside, the developer is transported into the virtual world by means of special glasses and the virtual models stand out three-dimensionally. The user checks the ergonomics, visibility and design of the interior and equipment. At a later stage it will be possible to go for a virtual drive through the city and the countryside.
Also in the second centre, the complete vehicle mock-up centre, the latest computer technology is used to power a projection onto two levels. Interactive, virtual applications such as the routing of wiring are checked in a similar way to the checks carried out in the "Cave”. This means that new wiring can be created or the ways of existing wiring can be modified.--During a meeting, for example.
Hardware, visualization space and offices cover a total area of around 4.500 square metres in the complete vehicle mock-up centre and the new project visualization centre. Intense work has been going on since April 2004 to complete both centres. The new buildings provide space for a total of 150 employees, creating 45 new jobs.
Volkswagen anticipates a reduction of up to 30% in cost and time through the use of the innovate 3D technology and the subsequent optimization of the product development process. Modifications during the planning and production stage had previously been associated with high levels of financial and time investment. Today, initial experiences of the virtual product can be analysed through computer simulations before models or tools are created for the actual production.